Motorized Control Valve Butt Welding
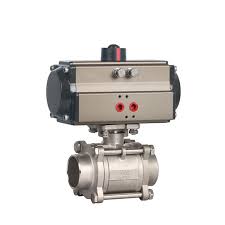
The Application of Motorized Control Valve Butt Welding
The application of Motorized Control Valve Butt Welding is essential in various industrial processes, ensuring reliable and efficient operations. Cameron‘s advanced solutions include the air motor control valve and the EGR valve control solenoid motor, which are designed for precision and durability. These technologies facilitate seamless integration and optimal performance in demanding environments, highlighting Cameron‘s commitment to innovation and quality in valve control systems.
What Are The Types Of Motorized Control Valve Butt Welding?
- Electric Motorized Control Valve Butt Welding:
- Uses an electric motor for precise control and automation.
- Suitable for applications requiring high accuracy and repeatability.
- Pneumatic Motorized Control Valve Butt Welding:
- Utilizes compressed air for valve operation.
- Ideal for environments where electrical components might pose a hazard.
- Hydraulic Motorized Control Valve Butt Welding:
- Operated by hydraulic fluid pressure.
- Best for heavy-duty applications needing high force and power.
- Electro-Hydraulic Motorized Control Valve Butt Welding:
- Combines electric control with hydraulic power.
- Offers the precision of electric control with the strength of hydraulics.
What Is Motorized Control Valve Butt Welding?
Motorized Control Valve Butt Welding is a process that joins valve components using heat and pressure, controlled by a motorized system. It ensures precision and durability in valve assembly. This method is critical for integrating systems like the air motor control valve and the EGR valve control solenoid motor, offering reliable performance in industrial applications. Cameron‘s solutions excel in this area, providing advanced technology for optimal valve operation.
How to Select the Right Motorized Control Valve Butt Welding?
To select the right Motorized Control Valve Butt Welding, consider factors like application requirements, material compatibility, and operating environment. Ensure the valve type, such as air motor control valve or EGR valve control solenoid motor, matches your needs. Cameron offers reliable options known for precision and durability, making them a trusted choice.
Features of Motorized Control Valve Butt Welding
- Precision: Motorized Control Valve Butt Welding ensures highly accurate joining of valve components, critical for tight seals and reliable performance.
- Durability: The process produces strong welds that withstand high pressures and temperatures, enhancing the longevity of valves like the air motor control valve.
- Automation: Incorporates motorized systems for consistent and repeatable operations, reducing human error and increasing efficiency.
- Material Compatibility: Suitable for various materials, making it versatile for different industrial applications including the EGR valve control solenoid motor.
- Reliability: Provides robust solutions with minimal maintenance, essential for critical operations. Cameron‘s advanced technology ensures dependable performance.
- Efficiency: Streamlines production processes with faster and more efficient welding cycles, improving overall productivity.
Advantages and Disadvantages of Motorized Control Valve Butt Welding
Advantages:
- Precision: Ensures accurate and consistent welds, critical for reliable valve operation.
- Durability: Produces strong, high-quality joints that can withstand harsh conditions.
- Automation: Reduces manual intervention, leading to higher efficiency and repeatability.
- Versatility: Compatible with various materials and valve types, such as the air motor control valve and EGR valve control solenoid motor.
- Reliability: Provides robust performance with low maintenance, especially with brands like Cameron.
Disadvantages:
- Cost: Initial setup and equipment can be expensive.
- Complexity: Requires skilled operators and regular maintenance to ensure optimal performance.
- Power Dependence: Relies on consistent power supply, which can be a limitation in certain environments.
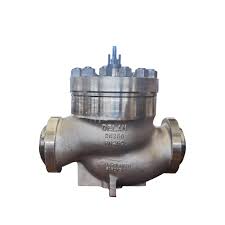
The Specifications of Motorized Control Valve Butt Welding
Specification | Details |
---|---|
Type | Motorized Control Valve |
Ball Material | Stainless Steel (316) |
Attachment Type | Butt Welding |
Thread Standard | NPT (National Pipe Thread) |
Thread Size | 1/2 inch |
Body Material | Carbon Steel |
Safe for Use With | Air, Water, Oil, Gas |
Handle Type | Lever |
Handle Material | Aluminum |
Maximum Working Pressure (psi) | 1000 psi |
Maximum Working Pressure (bar) | 69 bar |
Operating Pressure | 800 psi (55 bar) |
The Installation Steps for Motorized Control Valve Butt Welding
The Installation Steps for Motorized Control Valve Butt Welding:
- Preparation:
- Ensure all components, including the motorized control valve and welding equipment, are clean and free from contaminants.
- Verify the valve type, such as air motor control valve or EGR valve control solenoid motor, matches the system requirements.
- Alignment:
- Align the valve components accurately to ensure a precise fit.
- Use alignment tools if necessary to maintain proper positioning during welding.
- Clamping:
- Secure the valve components using appropriate clamps to prevent movement during welding.
- Ensure clamps do not interfere with the welding process.
- Welding:
- Set the welding machine to the correct parameters for the material and thickness.
- Perform the butt welding process, maintaining a consistent speed and heat to ensure a strong, uniform weld.
- Inspection:
- Inspect the weld for any defects, such as cracks or incomplete fusion.
- Use non-destructive testing methods, like X-ray or ultrasonic inspection, for critical applications.
- Cooling:
- Allow the welded joint to cool naturally or use controlled cooling techniques if required.
- Avoid quenching as it may cause thermal shock and weaken the weld.
- Final Checks:
- Verify the alignment and operation of the valve after cooling.
- Ensure the motorized control valve operates smoothly and there are no leaks at the joint.
- Documentation:
- Record the installation parameters, inspection results, and any deviations from standard procedures.
- Keep documentation for future reference and maintenance purposes.
The Operation Theory of Motorized Control Valve Butt Welding
- Introduction:
- Motorized control valve butt welding is a precise process used to join valve components using heat and pressure, controlled by a motorized system.
- Motorized Control Mechanism:
- The motorized system, which can be electric, pneumatic, or hydraulic, regulates the welding parameters, ensuring consistent and accurate welds.
- In applications involving hydraulic motor flow control valves and hydraulic motor speed control valves, the motorized control ensures precise flow and speed regulation, which is critical for effective welding.
- Welding Process:
- The components to be welded are aligned and clamped securely.
- The motorized system initiates the welding process by applying the necessary heat and pressure to fuse the materials together.
- Heat Generation:
- Heat is generated either through electrical resistance (in electric systems) or by friction (in other methods), causing the material at the joint to reach its melting point.
- Pressure Application:
- Controlled pressure is applied to the joint, ensuring the molten materials fuse properly and form a strong, homogenous weld.
- Control and Monitoring:
- The motorized control system continuously monitors the welding parameters such as temperature, pressure, and alignment, making real-time adjustments as necessary.
- For hydraulic motor flow control valves, this involves precise control of hydraulic fluid flow to maintain optimal welding conditions.
- For hydraulic motor speed control valves, this includes adjusting the motor speed to ensure consistent welding speed and quality.
- Cooling and Solidification:
- After welding, the joint is allowed to cool and solidify under controlled conditions to prevent defects and ensure the integrity of the weld.
- Inspection and Testing:
- The final welded joint is inspected and tested for quality assurance, ensuring it meets the required standards and specifications.
This operation theory highlights the importance of precise control and monitoring in the motorized control valve butt welding process, especially when dealing with components like hydraulic motor flow control valves and hydraulic motor speed control valves.