Ceramic Lined Globe Valve
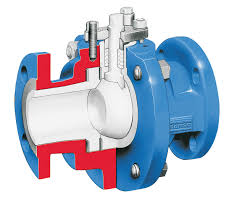
The Application of Ceramic Lined Globe Valve
The Corrosion-Resistant Ceramic Globe Valve from Cameron is a versatile and durable solution for a wide range of industrial applications. Featuring a ceramic-lined body, this valve provides exceptional resistance to aggressive chemicals, high temperatures, and abrasive media, making it an ideal choice for use in the High-Purity Ceramic Valve applications such as chemical processing, petrochemical refineries, and semiconductor manufacturing. The High-Temperature Ceramic Control Valve design ensures reliable performance even in demanding environments, ensuring precise flow control and tight shutoff. With its exceptional material properties, the Cameron ceramic-lined globe valve offers superior corrosion resistance, thermal stability, and a long service life, making it a cost-effective and efficient choice for industrial operators seeking a dependable flow control solution.
What Is Ceramic Lined Globe Valve?
A Ceramic Lined Globe Valve is a specialized type of industrial valve that features a ceramic-coated or ceramic-lined interior. The ceramic material, often made from advanced ceramics like alumina or silicon carbide, provides exceptional resistance to corrosion, erosion, and chemical attack. This makes the Ceramic Lined Globe Valve well-suited for handling aggressive fluids, high-purity media, and abrasive substances in demanding industrial applications such as chemical processing, petrochemical refineries, and semiconductor manufacturing. The ceramic lining also enhances the valve’s thermal stability, allowing it to withstand high temperatures without compromising its sealing integrity or performance. This unique combination of material properties ensures the Ceramic Lined Globe Valve delivers reliable, long-lasting service, making it a preferred choice for critical flow control operations in various industrial sectors.
How to Select the Right Ceramic Lined Globe Valve?
When selecting the appropriate Ceramic Lined Globe Valve for your application, several key factors should be considered. First, evaluate the chemical compatibility of the ceramic material with the specific fluids or media being handled. Additionally, assess the required temperature and pressure ratings to ensure the valve can withstand the operating conditions. The valve size, flow capacity, and end connections must also align with the system requirements. Other important considerations include the desired level of flow control, shutoff performance, and maintenance needs. By carefully matching the Ceramic Lined Globe Valve specifications to the unique demands of your industrial process, you can ensure reliable, efficient, and long-lasting flow control tailored to your specific application.
Features of Ceramic Lined Globe Valve
Chemical Resistance
The ceramic lining of the globe valve provides superior resistance to a wide range of corrosive chemicals, acids, and solvents, ensuring compatibility with diverse industrial media.
Thermal Stability
The valve’s ceramic components can withstand high temperatures without degradation, making it suitable for use in processes with elevated heat conditions.
Abrasion Resistance
The smooth, non-porous ceramic surfaces offer exceptional resistance to wear and abrasion, extending the valve’s service life even in applications with abrasive fluids.
Dimensional Stability
The low thermal expansion coefficients of ceramic materials help maintain the valve’s dimensional integrity and sealing performance across temperature fluctuations.
High Purity
The ceramic lining provides a clean, non-contaminating surface, making the valve ideal for use in high-purity applications, such as semiconductor manufacturing.
Reliable Sealing
The precision-engineered ceramic-to-ceramic sealing surfaces ensure a tight, leak-proof seal, providing reliable flow control and shutoff capabilities.
Advantages and Disadvantages of Ceramic Lined Globe Valve
Advantages of Ceramic Lined Globe Valve:
Corrosion Resistance: The ceramic lining offers superior resistance to a wide range of corrosive chemicals, acids, and solvents, making it suitable for harsh industrial environments.
Thermal Stability: Ceramic components can withstand high temperatures without degradation, expanding the valve’s application range to include processes with elevated heat conditions.
Abrasion Resistance: The smooth, non-porous ceramic surfaces provide exceptional resistance to wear and abrasion, extending the valve’s service life in applications with abrasive fluids.
High Purity: The ceramic lining ensures a clean, non-contaminating surface, making the valve ideal for use in high-purity applications, such as semiconductor manufacturing.
Reliable Sealing: The precision-engineered ceramic-to-ceramic sealing surfaces ensure a tight, leak-proof seal, providing reliable flow control and shutoff capabilities.
Disadvantages of Ceramic Lined Globe Valve:
Brittleness: Ceramic materials are generally more brittle compared to metallic components, which can make them susceptible to cracking or fracturing under high stress or impact.
Thermal Shock Sensitivity: Rapid temperature changes can potentially cause thermal shock and damage the ceramic lining, requiring careful consideration of temperature fluctuations in the application.
Higher Cost: Ceramic-lined valves typically have a higher initial cost compared to traditional metal-bodied valves, which can be a factor in some budget-conscious projects.
Limited Size Range: Ceramic-lined valves may not be available in the full range of sizes that can be found for metal-bodied valves, potentially limiting their application in certain systems.
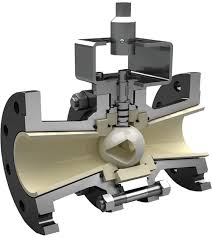
The Specifications of Ceramic Lined Globe Valve
Specification | Details |
---|---|
Type | Globe Valve |
Ball Material | Alumina Ceramic |
Attachment Type | Threaded |
Thread Standard | ANSI B1.20.1 |
Thread Size | 1/2″ NPT |
Body Material | Carbon Steel with Ceramic Lining |
Safe for Use With | Acids, Corrosive Chemicals, High-Purity Fluids |
Handle Type | Lever |
Handle Material | Stainless Steel |
Maximum Working Pressure | 300 psi |
Maximum Working Pressure | 20.7 bar |
Operating Pressure | 0-300 psi (0-20.7 bar) |
The Installation Steps for Ceramic Lined Globe Valve
1. Site Preparation:
Ensure the installation site is clean, free of debris, and provides sufficient clearance for valve operation and maintenance.
2. Valve Orientation:
Determine the correct orientation of the valve based on the flow direction, accessibility for operation, and compliance with any specific installation requirements.
3. Pipe Alignment:
Align the pipe flanges or threaded connections to ensure proper mating with the valve’s end connections. Verify that the pipe is properly supported and free of any strain or stress.
4. Threaded Installation:
For threaded valves, apply a suitable thread sealant or PTFE tape to the valve’s threads before hand-tightening the valve into the pipe fitting. Avoid over-tightening to prevent damage to the ceramic lining.
5. Flange Installation:
For flanged valves, position the valve between the mating pipe flanges and secure the connection using the appropriate bolts, nuts, and gaskets. Tighten the bolts in a star or crisscross pattern to ensure even loading on the flanges.
6. Leak Testing:
Perform a thorough leak test of the installed valve and surrounding connections using an appropriate method, such as air or water pressure testing, to ensure there are no leaks.
7. Functional Testing:
Operate the valve through its full range of motion to verify smooth and consistent operation. Adjust the packing or stem as needed to ensure proper sealing and actuation.
8. Documentation:
Record the installation details, including the valve’s serial number, date of installation, and any specific notes or observations, for future reference and maintenance purposes.
The Operation Theory of Ceramic Lined Globe Valve
Operation Theory of Ceramic Lined Globe Valve:
The Ceramic Lined Globe Valve operates based on the principles of fluid flow control. The valve uses a precision-engineered ceramic disc that moves up and down within the valve body to regulate the flow of the media. When the valve is open, the ceramic disc is lifted, allowing the fluid to pass through the valve. When the valve is closed, the ceramic disc is lowered, creating a tight seal and preventing the fluid from flowing.
The ceramic lining on the valve body and disc provides superior resistance to corrosion and abrasion, ensuring reliable operation even in harsh industrial environments. The smooth, non-porous ceramic surfaces also help to minimize turbulence and pressure drop, improving the valve’s flow characteristics.
Industrial Ceramic Valve Applications:
- Chemical Processing: Handling corrosive acids, bases, and solvents in chemical manufacturing and refining operations.
- Semiconductor Manufacturing: Providing high-purity flow control in semiconductor fabrication facilities.
- Pharmaceutical Production: Ensuring reliable flow control of sensitive pharmaceutical ingredients and formulations.
- Power Generation: Controlling the flow of water, steam, and other fluids in power plant operations.
- Food and Beverage Processing: Regulating the flow of food-grade liquids, slurries, and other food-safe media.
- Wastewater Treatment: Managing the flow of corrosive and abrasive fluids in water and wastewater treatment plants.
Ceramic Valve Installation Guide:
- Carefully inspect the valve and its components to ensure there are no visible defects or damage.
- Determine the correct orientation of the valve based on the flow direction and accessibility for operation.
- Clean the pipe connections and apply a suitable thread sealant or gasket material to ensure a tight seal.
- Securely install the valve, either by threading it into the pipe fittings or by bolting the flanges to the mating pipe flanges.
- Perform a thorough leak test to verify the integrity of the valve and pipe connections.
- Operate the valve through its full range of motion to ensure smooth and consistent operation.
- Document the installation details, including the valve’s serial number and any specific notes or observations.
- Implement a regular maintenance schedule to ensure the valve continues to function reliably over its lifetime.