DIN Lift Check Valve
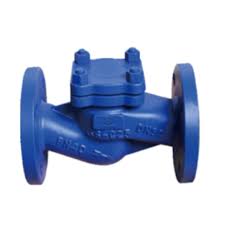
The Application of DIN Lift Check Valve
Introducing the versatile range of DIN Lift Check Valves. Whether it’s the robust Cast Steel DIN Lift Check Valve, the standard-compliant DIN Standard Lift Check Valve, or the specialized Ring Seat Lift Check Valve, Cameron offers reliable solutions for diverse applications. These valves ensure fluid flow in one direction while preventing reverse flow, making them essential in industries such as oil and gas, petrochemicals, and water treatment. With Cameron’s commitment to quality and innovation, our DIN Lift Check Valves stand as trusted choices for ensuring system integrity and efficiency.
What Are The Types Of DIN Lift Check Valve?
- Cast Steel DIN Lift Check Valve:
- Constructed from cast steel materials, offering durability and reliability in various industrial applications.
- Stainless Steel DIN Lift Check Valve:
- Made from stainless steel, providing corrosion resistance and suitability for applications requiring hygiene and cleanliness.
- Ring Seat DIN Lift Check Valve:
- Features a ring seat design for improved sealing performance, minimizing the risk of leakage.
- Flanged Connection DIN Lift Check Valve:
- Equipped with flanged connections for easy installation and secure attachment to pipelines or systems.
- Bellows Seal DIN Lift Check Valve:
- Incorporates bellows seals for enhanced sealing capability, particularly suitable for applications requiring tight shut-off and minimal leakage.
What Is DIN Lift Check Valve?
The DIN Lift Check Valve is a type of industrial valve designed to allow fluid flow in one direction while preventing reverse flow. Complying with DIN standards, it features a disc or piston that lifts off its seat to allow flow and closes under reverse flow conditions, ensuring system integrity. Widely used in various industries such as oil and gas, petrochemicals, and water treatment, it provides reliable fluid control and prevents backflow issues.
How to Select the Right DIN Lift Check Valve?
Selecting the right DIN Lift Check Valve involves considering factors such as flow rate, operating pressure, and fluid compatibility. Determine the required valve size and connection type to ensure compatibility with the pipeline. Consider any specific features needed, such as bellows seals for enhanced sealing or flanged connections for easy installation. Consulting with a reputable supplier can aid in selecting the most suitable DIN Lift Check Valve for your application.
Features of DIN Lift Check Valve
- Design: DIN lift check valves are engineered with a vertical lift mechanism.
- Body: The body is typically constructed from durable materials such as cast iron, cast steel, or stainless steel.
- Flange: It features a flanged end connection for easy installation and maintenance.
- Disc: The valve incorporates a spring-loaded disc, ensuring reliable sealing against reverse flow.
- Operation: These valves operate automatically, relying on fluid pressure to open and close.
- Application: Widely used in various industries including water treatment, chemical processing, and petrochemical.
- Size Range: Available in a diverse range of sizes to accommodate different flow rates and pipeline requirements.
- Pressure Rating: DIN lift check valves come in various pressure ratings, ensuring compatibility with different system pressures.
- Standards: Designed in accordance with DIN standards, ensuring conformity and reliability.
- Maintenance: Simple design facilitates easy inspection, cleaning, and repair, minimizing downtime.
Advantages and Disadvantages of DIN Lift Check Valve
Advantages:
- Reliability: Offers reliable prevention of reverse flow, ensuring system integrity.
- Automatic Operation: Operates automatically without the need for external control, reducing manual intervention.
- Low Pressure Drop: Minimal pressure drop across the valve, optimizing system efficiency.
- Diverse Applications: Suitable for various industries and applications due to its versatility.
- Conformance: Manufactured according to DIN standards, ensuring quality and compatibility.
Disadvantages:
- Limited Suitability: May not be suitable for applications requiring precise flow control.
- Potential for Water Hammer: In certain conditions, the closing of the valve can generate water hammer effects.
- Maintenance Requirements: While generally low maintenance, periodic inspection and cleaning are necessary to ensure proper functioning.
- Initial Cost: Depending on size and material, initial costs may be higher compared to other types of check valves.
- Size Limitations: Larger sizes may be limited in availability and may require custom fabrication, leading to longer lead times.
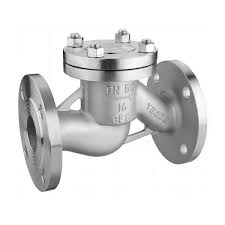
The Specifications of DIN Lift Check Valve
Specification | Value |
---|---|
Type | Lift Check Valve (DIN) |
Ball Material | Not Applicable |
Attachment Type | Flanged |
Thread Standard | DIN |
Thread Size | Not Applicable |
Body Material | Cast Iron, Ductile Iron, Carbon Steel |
Safe for Use With | Water, Oil, Gas |
Handle Type | Not Applicable |
Handle Material | Not Applicable |
Maximum Working Pressure | 16 bar (232 psi) |
Operating Pressure | Dependent on Application |
The Installation Steps for DIN Lift Check Valve
- Preparation:
- Gather all necessary tools and equipment: wrenches, pipe dope, Teflon tape, etc.
- Ensure the work area is clean and free from debris.
- Valve Inspection:
- Examine the valve for any signs of damage or defects.
- Check that the valve size matches the pipe size.
- Valve Positioning:
- Determine the correct orientation of the valve (flow direction arrow).
- Position the valve in place within the pipeline.
- Flange Connection:
- Align the valve flanges with the corresponding pipe flanges.
- Insert and tighten the bolts evenly to secure the connection.
- Threaded Connection (if applicable):
- Wrap the male threads with Teflon tape.
- Screw the valve into the threaded pipe fitting, ensuring a tight seal.
- Welding (if applicable):
- Clean the welding surfaces of both the valve and the pipe.
- Weld the valve to the pipeline according to welding specifications.
- Testing:
- Perform a pressure test to ensure the valve operates correctly and there are no leaks.
- Open and close the valve several times to check for smooth operation.
- Final Checks:
- Inspect the installation for any loose connections or irregularities.
- Verify that all valves are properly labeled for easy identification.
The Operation Theory of DIN Lift Check Valve
DIN Lift Check Valve: The DIN Lift Check Valve operates on a simple but effective principle to prevent backflow in a piping system. When fluid flows in the desired direction, the pressure of the fluid lifts the internal mechanism of the valve, allowing the fluid to pass through. This mechanism typically consists of a disc or a piston-like element. However, when there is a reversal in flow direction or a decrease in pressure downstream, gravity and/or a spring mechanism causes the valve to close, effectively blocking the flow in the opposite direction. This design ensures that the system maintains its desired flow direction and prevents any backflow.
Flanged Connection Lift Check Valve: Similar to the DIN Lift Check Valve, the Flanged Connection Lift Check Valve also operates based on the principle of preventing backflow. However, it includes flanged connections that facilitate a secure and leak-proof connection between the valve and the pipeline. These flanges are bolted together, ensuring that the valve remains firmly in place, even under high-pressure conditions. This type of valve is commonly used in applications where a reliable and robust connection is essential, such as in industrial processes, water distribution systems, and wastewater treatment plants.
Stainless Steel Lift Check Valve: The Stainless Steel Lift Check Valve shares the same operational theory as other lift check valves but is constructed using stainless steel materials. Stainless steel offers exceptional resistance to corrosion and chemical damage, making it ideal for applications involving corrosive fluids or environments. The valve’s internal mechanism operates in the same manner as described for the DIN Lift Check Valve, providing reliable backflow prevention while offering the added benefit of enhanced durability and longevity due to its stainless steel construction. These valves find extensive use in industries such as petrochemical, chemical processing, food and beverage, pharmaceuticals, and marine applications.