Monoblock Wafer Type Ball Valve
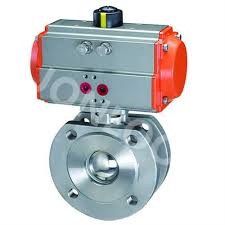
The Application of Thin Ball Valve
The Thin Ball Valve is a versatile and reliable valve solution for a wide range of industrial applications. For corrosive environments, the Corrosion-Resistant Monoblock Wafer Ball Valve from Cameron offers exceptional durability, featuring a one-piece body design that eliminates potential leak paths. In applications where space is limited, the Seamless Monoblock Wafer Ball Valve provides a compact footprint without sacrificing performance. When high-pressure conditions are a concern, the High-Pressure Thin Monoblock Wafer Ball Valve from Cameron is engineered to withstand pressures up to 1000 psi, making it a suitable choice for demanding process systems. Across a variety of industries, from chemical processing to oil and gas, the Thin Ball Valve’s precise flow control, ease of installation, and robust construction make it an excellent choice for optimizing fluid management and ensuring system integrity.
What Are The Types Of Thin Ball Valve?
1. Wafer-Type Thin Ball Valve:
Wafer-style Thin Ball Valves are designed to be installed between two pipe flanges, creating a compact and space-saving valve solution. The valve body sits between the flanges and is secured in place by the flange bolts, eliminating the need for separate end connections.
2. Lug-Type Thin Ball Valve:
Lug-type Thin Ball Valves have bolt holes in the valve body that allow it to be directly bolted to the pipe flanges. This design provides a sturdy connection and is suitable for applications where the valve needs to support piping loads.
3. Threaded-End Thin Ball Valve:
Threaded-end Thin Ball Valves have male or female threaded ends that can be directly screwed into the pipe connections. This type is useful for smaller pipe sizes where flanged connections may not be practical.
4. Flanged-End Thin Ball Valve:
Flanged-end Thin Ball Valves have integral flanges on the valve body, allowing them to be bolted directly to matching pipe flanges. This design provides a secure and leak-tight connection.
5. Sanitary/Hygienic Thin Ball Valve:
Sanitary or hygienic Thin Ball Valves are designed for applications in the food, beverage, and pharmaceutical industries, where cleanliness and sterility are critical. These valves often have special surface finishes and connection options to meet industry standards.
What Is Thin Ball Valve?
A Thin Ball Valve is a specialized type of ball valve that is characterized by its compact and streamlined design. Unlike traditional ball valves, Thin Ball Valves have a significantly reduced profile, making them well-suited for applications where space is limited. The valve body is typically thinner, and the overall dimensions are smaller compared to standard ball valves of the same size. This slim profile allows the Thin Ball Valve to be easily installed in tight spaces, such as in crowded piping systems or where access is restricted. Despite their compact size, Thin Ball Valves maintain the same reliable and precise flow control capabilities as their larger counterparts, making them a popular choice across a variety of industries, including chemical processing, oil and gas, and water treatment. The thin design, combined with features like corrosion resistance and high-pressure ratings, make Thin Ball Valves a versatile and efficient valve solution for a wide range of applications.
How to Select the Right Thin Ball Valve?
When selecting the appropriate Thin Ball Valve for a specific application, there are several key factors to consider. Firstly, it is important to assess the operating conditions, such as pressure, temperature, and the media being handled, to ensure the valve is rated for the intended service. Additionally, the size and connection type (wafer, lug, threaded, or flanged) must match the system requirements. The material of construction, particularly the ball and seat, should be compatible with the process fluids to prevent corrosion or chemical attack. For applications where hygiene and cleanliness are critical, such as in the food and pharmaceutical industries, sanitary Thin Ball Valves with specialized surface finishes may be necessary. By carefully evaluating these important parameters, users can select the Thin Ball Valve that best meets the demands of their particular system, ensuring reliable and efficient performance.
Features of Thin Ball Valve
Compact Design:
Thin Ball Valves are designed with a slimmer profile compared to traditional ball valves, allowing for easy installation in tight spaces and space-constrained applications.
Corrosion Resistance:
The Corrosion-Resistant Monoblock Wafer Ball Valve features a one-piece body design that eliminates potential leak paths, providing exceptional durability in corrosive environments.
High-Pressure Capability:
The High-Pressure Thin Monoblock Wafer Ball Valve is engineered to withstand pressures up to 1000 psi, making it suitable for demanding process systems.
Seamless Construction:
The Seamless Monoblock Wafer Ball Valve design offers a compact footprint without sacrificing performance, providing a reliable and leak-tight solution.
Precision Flow Control:
Thin Ball Valves offer precise flow control, allowing for accurate regulation of fluid and gas flow in a variety of industrial applications.
Easy Installation:
The compact and versatile design of Thin Ball Valves simplifies the installation process, reducing time and labor requirements.
Advantages and Disadvantages of Thin Ball Valve
Advantages of Thin Ball Valve:
Space-Saving Design:
The slim profile of Thin Ball Valves allows for easy installation in tight spaces, making them a suitable choice for applications with limited available space.
Corrosion Resistance:
Many Thin Ball Valve models, such as the Corrosion-Resistant Monoblock Wafer Ball Valve, are designed to withstand harsh, corrosive environments, ensuring reliable long-term performance.
High Pressure Capability:
The High-Pressure Thin Monoblock Wafer Ball Valve can handle pressures up to 1000 psi, making it a versatile option for demanding process systems.
Precise Flow Control:
Thin Ball Valves offer precise and reliable flow control, allowing for accurate regulation of fluid and gas flow in a variety of industrial applications.
Ease of Installation:
The compact and streamlined design of Thin Ball Valves simplifies the installation process, reducing the time and labor required.
Disadvantages of Thin Ball Valve:
Limited Size Range:
Thin Ball Valves are typically available in smaller pipe sizes, which may not be suitable for larger-scale applications that require higher flow rates.
Potential for Leakage:
If not properly maintained or installed, the slim design of Thin Ball Valves may increase the risk of potential leaks, especially in high-pressure or high-temperature environments.
Higher Cost:
Thin Ball Valves can be more expensive compared to traditional ball valve designs, due to their specialized manufacturing and material requirements.
Restricted Flow Capacity:
The compact nature of Thin Ball Valves may result in a lower flow capacity compared to larger, standard ball valve designs.
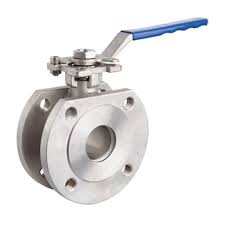
The Specifications of Thin Ball Valve
Specification | Details |
---|---|
Type | Wafer-Type Thin Ball Valve |
Ball Material | 316 Stainless Steel |
Attachment Type | Wafer-Style |
Thread Standard | NPT |
Thread Size | 1/2″ |
Body Material | 316 Stainless Steel |
Safe for Use With | Water, Oil, Gas, Chemicals |
Handle Type | Lever Handle |
Handle Material | Vinyl Coated Steel |
Maximum Working Pressure (psi) | 800 psi |
Maximum Working Pressure (bar) | 55 bar |
Operating Pressure | 0-800 psi (0-55 bar) |
The Installation Steps for Thin Ball Valve
Step 1: Inspect the Valve
Carefully inspect the Thin Ball Valve to ensure there is no visible damage or defects. Check that all components are present and in good condition.
Step 2: Prepare the Pipe System
Clean and prepare the pipe system where the Thin Ball Valve will be installed. Remove any debris, scale, or other contaminants to ensure a proper seal.
Step 3: Determine the Valve Orientation
Identify the desired flow direction and install the Thin Ball Valve accordingly. The valve should be positioned with the flow arrow pointing in the correct direction.
Step 4: Position the Valve
Center the Thin Ball Valve between the two pipe flanges, ensuring the bolt holes are properly aligned.
Step 5: Secure the Valve
Insert the bolts through the valve body and pipe flanges, then tighten the nuts in a crisscross pattern to the recommended torque specifications.
Step 6: Check the Valve Operation
Operate the valve handle to ensure smooth and complete opening and closing. Verify that the valve is functioning correctly.
Step 7: Test for Leaks
Pressurize the system and check for any leaks around the valve body and connections. Tighten the bolts if necessary to achieve a tight seal.
Step 8: Insulate and Protect (if required)
If the application requires insulation or additional protection, ensure the Thin Ball Valve is properly insulated and shielded to maintain the desired operating conditions.
The Operation Theory of Thin Ball Valve
Operation Theory of Thin Ball Valve
The operation of a Thin Ball Valve is based on the rotational movement of a spherical ball within the valve body. When the valve is in the open position, the bore of the ball aligns with the pipe, allowing fluid to flow freely through the valve. By rotating the ball 90 degrees, the flow is interrupted, and the valve is in the closed position.
The compact, space-saving design of Thin Ball Valves is achieved through a monoblock construction, where the body and end connections are integrated into a single, seamless unit. This design eliminates potential leak paths, enhancing the valve’s durability and reliability.
Sanitary Monoblock Wafer Ball Valve
The Sanitary Monoblock Wafer Ball Valve is specifically designed for applications requiring high levels of cleanliness and hygiene, such as in the food, beverage, and pharmaceutical industries. The valve features a smooth, polished interior surface and specialized materials that are resistant to corrosion and chemical attack, ensuring the purity of the processed media. The monoblock construction and sanitary design minimize the risk of contamination, making it an ideal choice for sensitive processing environments.
Chemical Pipeline Monoblock Wafer Ball Valve
The Chemical Pipeline Monoblock Wafer Ball Valve is engineered to withstand the demands of harsh chemical processing environments. The valve’s one-piece body design and carefully selected materials, such as high-performance alloys, provide exceptional resistance to corrosion and chemical attack. This robust construction ensures the valve’s reliability and longevity, even when handling aggressive media found in various industrial chemical applications.
The operation principle of these specialized Thin Ball Valve models remains the same, with the ball rotating to control the flow. However, the enhanced design features and material selections ensure they can safely and reliably operate in the specific conditions required for sanitary and chemical processing applications.