Positive Safety Swing Check Valves
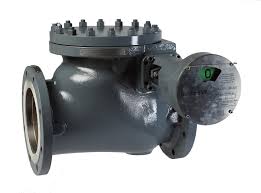
The Application of Safety Swing Check Valves
Introducing Cameron’s Safety Swing Valve, also known as a Non-Return Valve or Industrial Safety Valve. These valves are crucial components in various industries, preventing the backflow of fluids and ensuring system safety. Cameron’s Safety Swing Check Valves offer reliable performance and durability, meeting the highest industry standards. Used in pipelines, refineries, chemical plants, and more, these valves provide essential protection against fluid reversal, safeguarding equipment and processes. Trust Cameron for superior quality and performance in Safety Swing Check Valves, ensuring the integrity and efficiency of your operations.
What Are The Types Of Safety Swing Check Valves?
- Spring-loaded Swing Check Valve: These valves feature a spring mechanism that assists in closing the valve quickly, preventing backflow and ensuring tight shut-off.
- Gravity-operated Swing Check Valve: Gravity-operated valves rely on the weight of the closure element to ensure proper sealing when there is no forward flow, making them suitable for low-pressure applications.
- Lever and Weight Swing Check Valve: These valves utilize a lever and weight mechanism to facilitate the opening and closing of the valve, providing reliable operation even in high-pressure systems.
- Dual Disc Swing Check Valve: Dual disc valves feature two discs that swing open and closed, offering improved sealing and reduced pressure drop compared to traditional swing check valves.
- Silent Swing Check Valve: Silent check valves are designed with special features to minimize noise and water hammer effects during operation, making them ideal for applications where noise reduction is important.
What Is Safety Swing Check Valves?
A Safety Swing Check Valve is a type of check valve designed to prevent backflow in pipelines. It features a swinging disc or flap that opens in the direction of flow and closes to prevent reverse flow. These valves are crucial for maintaining system integrity and preventing damage to equipment. They find applications in industries such as oil and gas, water treatment, and chemical processing, ensuring the safety and efficiency of fluid flow systems.
How to Select the Right Safety Swing Check Valves?
Selecting the right Safety Swing Check Valve involves considering factors such as flow rate, pressure, temperature, and fluid compatibility. Determine the specific requirements of your application and choose a valve with appropriate size, material, and operating mechanism. Consider factors like backflow pressure, installation orientation, and maintenance requirements to ensure optimal performance and longevity. Consulting with a valve expert can also help in making the right selection for your system’s needs.
Features of Safety Swing Check Valves
- Backflow Prevention: Prevents reverse flow of fluids in pipelines, ensuring system integrity and preventing damage to equipment.
- Swing Disc Design: Utilizes a swinging disc or flap that opens in the direction of flow and closes to prevent backflow, providing reliable operation.
- Versatility: Suitable for various applications and industries including oil and gas, water treatment, chemical processing, and HVAC systems.
- Durable Construction: Built with robust materials such as stainless steel, carbon steel, or ductile iron, ensuring longevity and reliability in harsh environments.
- Low Pressure Drop: Offers minimal resistance to flow, reducing pressure drop and energy consumption in the system.
- Compact Design: Requires minimal space for installation, making it suitable for applications with limited space availability.
- Easy Maintenance: Simple design allows for easy inspection and maintenance, reducing downtime and operational costs.
- Optional Features: Available with optional features such as spring-assisted closure, lever and weight mechanism, or silent operation to suit specific application requirements.
Advantages and Disadvantages of Safety Swing Check Valves
Certainly, here are the advantages and disadvantages of Safety Swing Check Valves:
Advantages:
- Efficient Backflow Prevention: Prevents reverse flow of fluids, ensuring system integrity and preventing damage to equipment.
- Versatility: Suitable for a wide range of applications and industries, including oil and gas, water treatment, chemical processing, and HVAC systems.
- Reliable Operation: Utilizes a swinging disc or flap that opens and closes smoothly, providing reliable backflow prevention.
- Durable Construction: Built with robust materials such as stainless steel or carbon steel, ensuring longevity and reliability in harsh environments.
- Low Pressure Drop: Offers minimal resistance to flow, reducing pressure drop and energy consumption in the system.
Disadvantages:
- Flow Restriction: May cause some restriction to flow due to the swinging disc design, particularly in high-flow applications.
- Potential for Water Hammer: Rapid closure of the valve may lead to water hammer effects, potentially causing damage to pipes and equipment.
- Limited to Horizontal Installation: Some swing check valves are limited to horizontal installation, restricting their application in vertical pipelines.
- Maintenance Requirements: May require periodic maintenance to ensure proper operation, including inspection and potential replacement of wearing parts.
- Limited Effectiveness at Low Flow Rates: May not be as effective in preventing backflow at low flow rates, potentially leading to leakage.
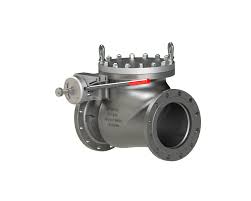
The Specifications of Safety Swing Check Valves
Specification | Details |
---|---|
Type | Safety Swing Check Valve |
Ball Material | Stainless Steel |
Attachment Type | Threaded |
Thread Standard | ANSI/ASME B1.20.1 |
Thread Size | 1/2 inch |
Body Material | Brass |
Safe for Use With | Water, Oil, Gas |
Handle Type | Lever |
Handle Material | Zinc Alloy |
Maximum Working Pressure psi | 200 psi |
Maximum Working Pressure bar | 13.8 bar |
Operating Pressure | 10-150 psi |
The Installation Steps for Safety Swing Check Valves
- Preparation: Gather all necessary tools and equipment including wrenches, pipe sealant, and Teflon tape.
- Shut Off Supply: Turn off the main water, oil, or gas supply to the system where the valve will be installed.
- Inspect Valve: Check the valve for any damage or defects before installation.
- Clean Pipes: Ensure the pipes where the valve will be installed are clean and free of debris.
- Apply Sealant: Wrap the male threads of the valve with Teflon tape or apply pipe sealant to ensure a proper seal.
- Thread Connection: Thread the valve onto the pipe using a wrench, ensuring it is tightened securely.
- Alignment: Ensure the valve is aligned properly with the flow direction indicated by the arrow on the valve body.
- Final Tightening: Use a wrench to make a final tight connection, being careful not to over-tighten and damage the valve.
- Test: Turn the supply back on and test the valve to ensure it opens and closes properly, and there are no leaks.
- Secure Valve: Once tested, secure the valve in its final position using pipe straps or brackets.
The Operation Theory of Safety Swing Check Valves
Operation Theory of Safety Swing Check Valves:
Safety swing check valves are designed to allow fluid flow in one direction while preventing reverse flow. They typically consist of a hinged flap or disc inside the valve body that swings open to allow fluid to pass through in the desired direction and closes to prevent backflow. The operation of safety swing check valves is based on fluid pressure and the force of gravity.
Here’s how they work:
- Forward Flow: When fluid flows in the desired direction, it exerts pressure on the hinged flap or disc, pushing it open against gravity. This allows the fluid to pass through the valve with minimal resistance.
- Prevention of Backflow: If there is any attempt of reverse flow, the pressure of the fluid pushes the flap or disc against the valve seat, sealing off the passage and preventing the backflow of fluid. This action is crucial for maintaining the integrity and safety of pipelines and systems.
Safety swing check valves are commonly used in various industries such as oil and gas, water treatment, and chemical processing to prevent damage to equipment and ensure the safety and efficiency of fluid flow systems.
Now, let’s move on to Pipeline Safety Valve and Hydraulic Swing Valve:
Pipeline Safety Valve:
A pipeline safety valve is a type of valve designed to automatically open and relieve excess pressure from a pipeline system to prevent overpressure situations. These valves typically operate based on the pressure inside the pipeline exceeding a preset threshold. When the pressure surpasses this threshold, the valve opens to release the excess pressure, thus safeguarding the pipeline and associated equipment from potential damage.
Hydraulic Swing Valve:
Hydraulic swing valves are valves that utilize hydraulic pressure to control the opening and closing of the valve. These valves typically consist of a disc or flap that swings open or closed based on changes in hydraulic pressure. They are commonly used in hydraulic systems to regulate the flow of fluid and maintain system stability and safety.
Both pipeline safety valves and hydraulic swing valves play critical roles in various industrial applications where the control and regulation of fluid flow and pressure are essential for operational efficiency and safety.