Orbit Ball Valve
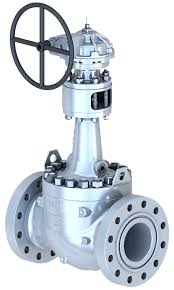
The Application of Orbit Ball Valve
The Rotork Orbit Ball Valve stands at the forefront of fluid control solutions, alongside industry leaders like Barton 200AS, ITT Barton 288C, and Barton 247C. Designed for precision and reliability, it excels in critical applications where tight shut-off and precise flow control are essential. With its innovative design, it ensures optimal performance and longevity, meeting the rigorous demands of various industries. Cameron Orbit Ball Valve is another notable competitor in the market. Whether in oil and gas, petrochemical, or power generation, the Orbit Ball Valve offers superior performance and durability, making it a preferred choice for discerning professionals.
slurry valve types
cooling tower valves suppliers
cooling tower valves company
idle control valve
Advantages of Orbit Ball Valve
- No Seal Abrasion: Orbit valves eliminate seal abrasion by using a tilt-and-turn movement, preventing wear between sealing surfaces.
- Individual Seat Design: They feature individual, fixed seats that seal in both directions, resolving issues associated with trapped pressure.
- Maximal Flow: With full port or reduced port apertures, orbit valves increase system pumping efficiency and minimize erosion issues.
- Extended Lifespan: These valves outlast conventional gate valves, plug valves, and globe valves, reducing maintenance costs and plant downtime.
- Injectable Packing: Stem stuffing substance is pumped through the packing fitting to regulate fugitive emissions during maintenance.
- Top-entry Structure: Facilitates maintenance with in-line examination and repair after system depressurization.
- Self Cleaning: Orbit valves feature a design that allows product flow to wash away material from the seat, ensuring cleanliness.
- Two Stem Guides: Strong guide pins and solidified stem openings regulate the lift-and-turn motion of the stem.
- Low-torque Performance: Seal rubbing is eliminated, enabling easy valve rotation.
- Automatic Cam Closure: The cam angle at the stem’s end provides a mechanically powered seal closure.
- Wear-resistant Core: Made of a tough, polished substance, the core face withstands demanding use and resists wear, maintaining sealing integrity.
How does an Orbit Ball Valve Work?
- Sealing Mechanism: The valve features individual, fixed seats that seal in both directions, preventing any pressure from being trapped between the seals.
- Ball Rotation: When the handle is turned, the ball rotates within the valve body. This movement allows the ball to tilt and turn, creating a 360-degree flow path around the core exterior.
- Flow Regulation: As the ball rotates, it controls the flow of fluid through the valve. The design ensures that the flow washes away any material from the seat, preventing build-up and ensuring smooth operation.
- Stem Movement: The stem of the valve is lifted and turned by strong guide pins and solidified stem openings. This movement is regulated to ensure proper sealing and flow control.
- Low Torque Operation: With the elimination of seal abrasion, the valve offers low-torque performance, making it easy to operate.
- Automatic Closure: At the stem’s deeper end, a cam angle provides a mechanically powered seal closure, ensuring tight shut-off when the valve is closed.
The Specifications of Orbit Ball Valve
Specification | Details |
---|---|
Type | Orbit Ball Valve |
Ball Material | Stainless Steel |
Attachment Type | Flanged, Threaded, Welded |
Thread Standard | ASME B1.20.1, ISO 7/1, BS 21, DIN 2999, etc. |
Thread Size | 1/2″ – 10″ (DN15 – DN250) |
Body Material | Carbon Steel, Stainless Steel, Alloy Steel |
Safe for Use With | Liquids, Gases, Steam |
Handle Type | Lever, Gear, Electric, Pneumatic |
Handle Material | Carbon Steel, Stainless Steel, Alloy Steel |
Maximum Working Pressure | Up to 3000 psi (Up to 207 bar) |
Operating Pressure | Based on valve rating and application requirements |
The Parameter of Orbit Ball Valve
- Type: Orbit Ball Valve
- Body Material: Carbon Steel, Stainless Steel, Alloy Steel
- Ball Material: Stainless Steel
- Seat Design: Individual, fixed seats for bidirectional sealing
- Attachment Type: Flanged, Threaded, Welded
- Thread Standard: ASME B1.20.1, ISO 7/1, BS 21, DIN 2999, etc.
- Thread Size: 1/2″ – 10″ (DN15 – DN250)
- Safe for Use With: Liquids, Gases, Steam
- Handle Type: Lever, Gear, Electric, Pneumatic
- Handle Material: Carbon Steel, Stainless Steel, Alloy Steel
- Maximum Working Pressure: Up to 3000 psi (Up to 207 bar)
- Operating Pressure: Based on valve rating and application requirements
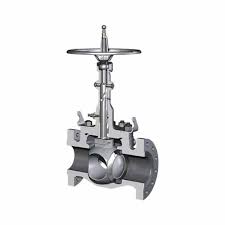
The Operation Theory of Orbit Ball Valve
The operation theory of the Cast Steel Floating Ball Valve involves a hollow ball that floats, controlled by the handle. When the handle is turned, the ball rotates within the valve body, regulating the flow of fluid. This design, favored by SKG Pneumatics Inc, ensures precise flow control and tight sealing. Compared to traditional valves like Barton 316C and Barton 224C, the floating ball valve offers enhanced reliability and longevity, making it ideal for various industrial applications.
The Parameters Table of Orbit Ball Valve
Component | Material |
---|---|
Body | Carbon Steel, Stainless Steel, Alloy Steel |
Ball | Stainless Steel |
Seat | PTFE, RPTFE, Nylon, Peek, etc. |
Stem | Stainless Steel |
Stem Seal | PTFE, Graphite |
Handle | Carbon Steel, Stainless Steel, Alloy Steel |
Bolting | Stainless Steel |
Gasket | Graphite, PTFE, etc. |
Bonnet | Carbon Steel, Stainless Steel, Alloy Steel |