Mining Valve
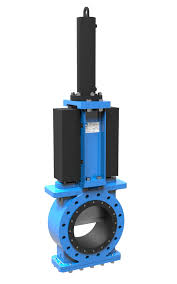
The Application of Mining Valve
Mining operations demand rugged, dependable valves that can withstand the harsh conditions found underground and in processing facilities. Brands like Cameron offer a comprehensive range of mining-specific valve solutions, including Mining Diaphragm Valves, Mining Gate Valves, and Mining-Specific Valves, designed to handle the unique challenges of the mining industry. These specialized valves are engineered to resist corrosion, abrasion, and extreme temperatures, ensuring reliable flow control and process efficiency in critical mining applications, such as slurry handling, water management, and chemical processing. By leveraging the latest advancements in material science and valve technology, Cameron provides mining operators with the resilient and high-performance valves they need to maintain safe, productive, and environmentally responsible operations.
valves for mining industry
ball valves for mining
valves for mining
What Are The Types Of Mining Valve?
- Slurry Valves: Designed to handle abrasive slurries and high-solids fluids encountered in mining operations. These valves often feature ceramic or rubber linings to resist wear.
- Knife Gate Valves: Used to isolate and control the flow of coarse solids, sludges, and other difficult-to-handle materials in mining processes.
- Ball Valves: Provide reliable on/off control and throttling capabilities for a variety of mining applications, including water, chemical, and process fluid handling.
- Diaphragm Valves: Offer tight shutoff and precision control for corrosive, abrasive, and high-purity fluids in mining and mineral processing.
- Pinch Valves: Squeeze the pipe closed to stop or restrict flow, making them well-suited for handling viscous, abrasive, and solids-laden liquids.
- Lined Valves: Feature protective linings like rubber, ceramic, or PTFE to withstand the harsh environments found in mines and mineral processing facilities.
- High-Performance Butterfly Valves: Provide fast, reliable actuation and tight shutoff for a range of mining applications, from water management to process control.
What Is Mining Valve?
Mining valves are specialized industrial valves designed to operate reliably and safely in the challenging environments encountered in mining operations. These valves are engineered to handle the abrasive slurries, corrosive fluids, high temperatures, and other extreme conditions that are common in the extraction, processing, and transportation of minerals, metals, and other geologic resources.
Mining valves often feature specialized materials, coatings, and designs to resist wear, corrosion, and other forms of degradation. Common types include slurry valves, knife gate valves, ball valves, and diaphragm valves, each tailored to address specific flow control and process requirements in the mining industry. By providing dependable performance and precise control, mining valves play a crucial role in maintaining safe, efficient, and environmentally responsible mining operations from exploration to production.
How to Select the Right Mining Valve?
When selecting the appropriate mining valve for an application, it is important to consider several key factors:
Flow Characteristics: Evaluate the flow rate, pressure, and composition of the fluid or slurry to be handled, ensuring the valve can provide the necessary control and capacity. Abrasion Resistance: Choose a valve design and materials, such as ceramic or hard rubber linings, that can withstand the wear and tear of abrasive media. Corrosion Resistance: Select a valve with materials and coatings that can resist the corrosive chemicals or environmental conditions present in the mining process. Temperature Tolerance: Ensure the valve can operate safely within the expected temperature range of the application. Actuation Requirements: Determine the appropriate valve actuation method, whether manual, pneumatic, or electric, based on the specific process needs.By carefully evaluating these critical parameters, mining operators can select the most suitable mining valve to ensure reliable, efficient, and safe flow control within their operations.
Features of Mining Valve
Abrasion Resistance:
Mining valves are designed with specialized materials and coatings to withstand the abrasive nature of slurries, ores, and other materials encountered in mining operations. This includes features like hard rubber or ceramic linings that can resist wear and erosion.
Corrosion Resistance:
The harsh chemical environments found in mining processes require valves made from corrosion-resistant materials, such as stainless steel, alloy, or specialized polymers, to maintain integrity and functionality.
Temperature Tolerance:
Mining valves must be able to operate reliably in a wide range of temperatures, from extreme cold in northern climates to high heat in smelting and processing facilities.
Robust Design:
The construction of mining valves prioritizes ruggedness and durability to withstand the vibrations, impacts, and other stresses inherent in mining equipment and infrastructure.
Specialized Sealing:
Effective sealing is critical in mining valves to prevent leaks of hazardous or environmentally sensitive materials. Advanced packing and gasket materials are used to maintain tight shutoff.
Flow Control Precision:
Mining valves often incorporate precise flow control mechanisms, such as high-performance actuators, to enable accurate regulation of slurries, liquids, and gases in processing operations.
Advantages and Disadvantages of Mining Valve
Advantages of Mining Valves:
Durability: Mining valves are engineered to withstand extreme conditions, including abrasion, corrosion, and high temperatures, ensuring reliable long-term performance.
Process Efficiency: The precision flow control and tight shutoff capabilities of mining valves help optimize process efficiency and reduce waste.
Safety: Mining valves play a critical role in containing and controlling hazardous materials, contributing to overall workplace and environmental safety.
Versatility: A diverse range of mining valve types, such as slurry valves, knife gate valves, and diaphragm valves, can be selected to meet specific application needs.
Disadvantages of Mining Valves:
Cost: Mining valves, with their specialized materials and design, can be more expensive than general-purpose industrial valves.
Maintenance: Regular maintenance and inspection are required to ensure the continued performance and safety of mining valves, which can be time-consuming and labor-intensive.
Complexity: The intricate design and operation of some mining valves, such as those with advanced actuation systems, may require specialized knowledge and skills for proper installation and troubleshooting.
Limited Availability: The relatively niche market for mining valves may result in limited availability and longer lead times for certain valve models or custom configurations.

The Specifications of Mining Valve
Specification | Detail |
---|---|
Type | Stainless Steel Ball Valve |
Ball Material | 316 Stainless Steel |
Attachment Type | Flanged |
Thread Standard | ASME B16.5 |
Thread Size | 4 inch |
Body Material | 316 Stainless Steel |
Safe for Use With | Slurry, Acids, Caustics, Oils, Gases |
Handle Type | Lever |
Handle Material | Stainless Steel |
Maximum Working Pressure (psi) | 500 |
Maximum Working Pressure (bar) | 34.5 |
Operating Pressure | 0-500 psi (0-34.5 bar) |
The Installation Steps for Mining Valve
Preparation:
- Ensure the valve, pipeline, and surrounding area are clean and free of any debris or obstructions.
- Verify that the valve size and pressure rating are compatible with the application requirements.
Flange Alignment:
- Position the valve between the two mating flanges, ensuring proper alignment of the bolt holes.
- Apply a thin layer of anti-seize compound to the bolt threads to facilitate future disassembly.
Bolt Tightening:
- Insert the bolts through the flange holes and hand-tighten them in a star or crisscross pattern.
- Using a calibrated torque wrench, tighten the bolts to the manufacturer’s recommended torque specification.
Valve Orientation:
- Rotate the valve to the desired orientation, ensuring the lever or actuator is accessible and the flow direction matches the intended process.
Valve Actuation:
- For manual operation, ensure the lever can move freely through its full range of motion.
- For automated operation, connect the appropriate pneumatic or electric actuator and verify proper functioning.
Leak Testing:
- Pressurize the pipeline and valve assembly to the maximum working pressure.
- Inspect all connections for any signs of leakage and tighten bolts as needed.
Final Inspection:
- Confirm the valve operates smoothly and that all safety features, such as limit switches, are functioning correctly.
- Document the installation details for future reference and maintenance purposes.
The Operation Theory of Mining Valve
Operation Theory of Mining Valves:
Mining valves operate on the basic principles of flow control, utilizing a variety of mechanisms to regulate the flow of fluids, slurries, and gases in mining operations. The core functionality of these valves is to allow, restrict, or completely shut off the passage of materials through the pipeline system.
The most common types of mining valves are:
- Ball Valves: These valves use a rotating ball with a bore to control the flow. The ball can be positioned to allow full flow, partial flow, or complete shut-off.
- Knife Gate Valves: These valves use a sliding gate or “knife” that moves perpendicular to the flow to open and close the valve. They are well-suited for slurry applications.
- Diaphragm Valves: These valves use a flexible diaphragm that flexes to open and close the flow path. They are effective for handling abrasive and corrosive media.
Mining Abrasion-Resistant Valves:
Abrasion-resistant mining valves are designed to withstand the wear and tear caused by the movement of coarse, gritty materials like ores, rocks, and sand. They feature specialized linings and coatings, such as ceramic, hard rubber, or tungsten carbide, that can resist erosion and maintain tight shutoff over extended periods of use.
Mining Corrosion-Resistant Valves:
Corrosion-resistant mining valves are engineered to operate in highly acidic, alkaline, or otherwise chemically aggressive environments. They are typically constructed from stainless steel, specialty alloys, or engineered polymers that can resist corrosion and maintain structural integrity under these challenging conditions.