Shower Diverter Valve
Valves quietly work in many different areas, even places you wouldn’t expect. They’re truly everywhere—power plants, drug factories, chemical plants, water treatment centers, heating and cooling systems, and even vehicle and airplane engines. You’ll find valves at home, work, and in amazing industrial locations. Some have complex designs and use cutting-edge tech and materials to withstand high pressures, harsh conditions, or detailed control tasks. Others are simple, controlling water flow in homes or enabling basic fluid control systems. Yet, most valves, even the critical and complex ones, share the same basic valve design principle and components.
In this discussion, we describe the basic valve components: Body, Bonnet, and Trim. We also explore four main components of valve trim: Disc, Seat, Stem, and Stem Packing. We also reference recent valve design innovations for these components as well!
The Design Function of a Valve Body
The valve body is the shell of the valve. It holds all the internal parts and helps control the flow of fluid. Its job is to be strong enough to handle system pressure and operating conditions. It lets the fluid flow through it and incorporates different valve connections in its design.
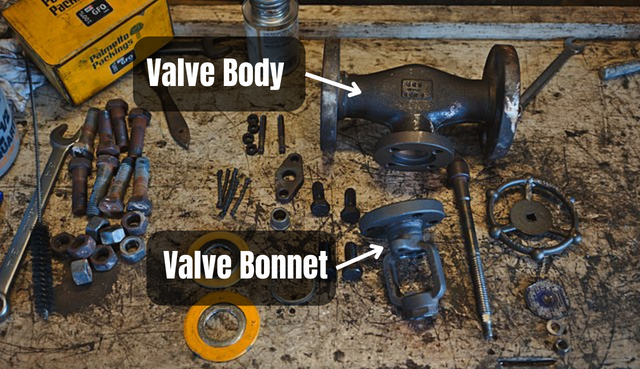
Steam Globe Valve Parts, licensed under CC BY 4.0, text added
The valve body material depends on factors such as the fluid it’s managing, pressure and temperature levels, and compatibility with other system parts. Commonly used materials include stainless steel, carbon steel, bronze, iron, and even non-metallic materials like PVC. Each material offers unique strengths like corrosion resistance, strength, and chemical compatibility, which allows valves to be used in countless situations. The body’s shape, port location, connection type, and other parts can vary depending on the valve type and the specific use. For instance, the actuator in valve design can affect the valve body’s construction.
Most innovations on valve body design are based around flow patterns for different fluids, including ports for actuation and monitoring controls, and new materials. Most often, a demanding process, like cryogenic applications leads to changes in the valve body’s design, manufacturing, and material.
The Essentials of Valve Bonnets
The valve bonnet is like a cap on top of the valve. It helps protect the internal components and ensure a tight seal, but the bonnet mainly exists to allow easy access for maintenance. It is an often overlooked part of a valves design. Bonnets can be made from various materials such as cast iron, cast steel, stainless steel, and bronze. Each provides different levels of durability, corrosion resistance, and heat tolerance. Valve bonnets can be joined in different ways—the most common ways being bolted, pressure sealed, and welded. Bolted covers are held tightly to the valve body with bolts. Pressure seal covers use internal pressure to make a stronger seal with the valve body. Welded bonnets are welded to the body, guaranteeing no leaks.
Recent innovations aim to improve reliability and reduce valve leakage, particularly fugitive emissions. Fugitive emissions occur when a valve leaks so slowly that it is visually undetectable. This can lead to a lot of unrealized gas emission! New bonnet designs, such as a modular bolted design, aim to reduce these fugitive emissions dramatically.
The Internal World of Valve Trim
Valve trim refers to a range of valve components. In fact all parts of a valve that are inside the valve are considered valve trim.
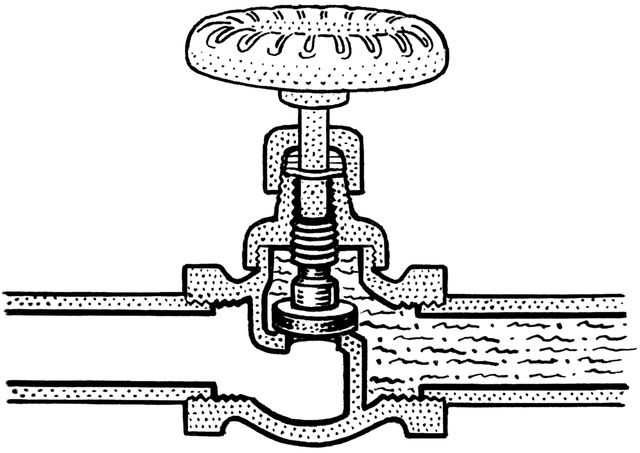
Globe Valve Cutaway, public domain image
The valve trim is, perhaps, the most critical part of a valve as it controls the fluid. Most differences between valves come down to the valve trim, more than the bonnet or body. In particular, control valve parts can differ drastically, which allows for valve solutions across many applications. The valve trim includes the disc, the seat, the stem, the stem packing, and any internal component. Here’s a brief description of these, and we’ll go into greater depth after.
- The disc is a key part of the valve trim. It controls how fluid moves through the valve. Depending on the need, discs are different shapes like flat, tilted, or spherical.
- The seat is the sealing surface where the disk comes into contact to prevent any leakage when the valve is closed. Seats are typically made from materials like a elastomer or metal to provide a lasting, tight seal.
- The stem is the part of the valve that connects the disc to the actuator. The stem opens and closes the valve disc. Stem design can vary substantially between different valves.
- The stem packing is a sealing material that surrounds the stem to prevent leaks along the stem’s axis. It also keeps the valve from leaking while the stem is moving.
Recent innovations in valve design and manufacturing of valve trim have tackled longstanding problems like cavitation in high pressure drop applications. Today, additive manufacturing techniques like 3D printing allows new parts to be designed and machined out of high-quality material, which will lead to impactful changes in valve design.
What Are A Few Common Types of Discs?
The design and shape of a valve’s disc greatly influences its performance, ability to control flow, and usefulness in particular situations. No matter the type—be it a butterfly, ball, gate valve, or anything else—the disc is crucial in determining each valve’s unique features and how it performs.
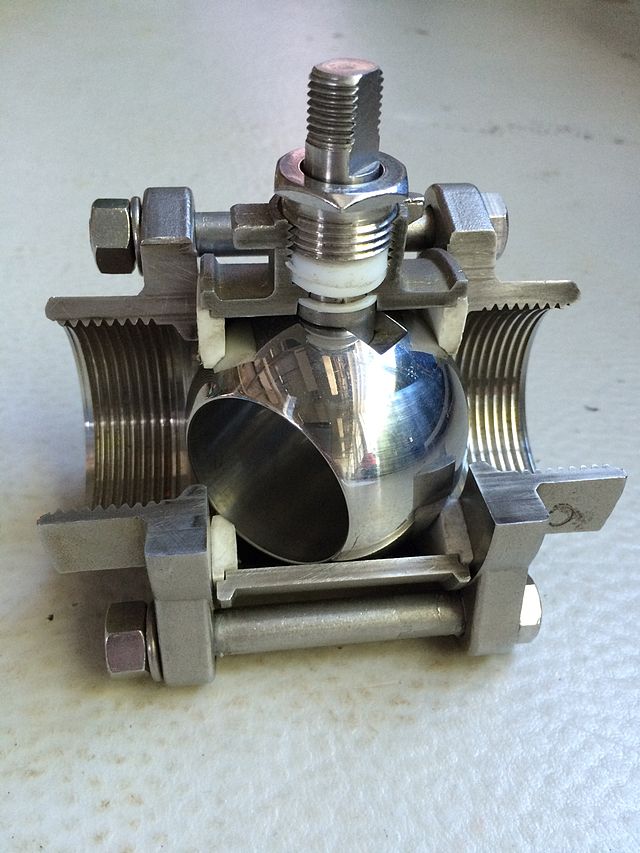
Ball Valve, licensed under CC BY 4.0, showcases the ball disc
Butterfly Discs
Butterfly discs consist of a circular plate with a pivot in the middle. It rotates to control the flow and is often used in low-pressure systems. In situations where there are high levels of turbulence or backflow, the butterfly disc may face performance issues.
Ball Discs
Next is the ball disc, shaped like a sphere, which offers excellent shutoff capabilities. Ball discs work great under high pressure and heat, so they’re used in industries like oil and gas.
Gate Discs
The gate disc is a flat or wedge-shaped piece that slides up and down to control the flow. This type ensures minimal pressure loss but has difficulties when the fluid contains solids.
Plug Disc
The plug disc is a cylindrical solid piece with a hole bored into it. When aligned, a plug disc allows flow, and when turned, it prevents flow. This design even appears in anAncient Roman Valve.
Globe Disc
The globe disc, typically flat or slightly convex, interacts with a valve seat in the valve body to regulate flow by moving perpendicular to the flow path.
What is a Valve Seat?
The valve seat appears in many valve designs, and it allows the disc to seal tightly, preventing leaks and loss of pressure.
Globe Valve Cutaway, Ball Valve, licensed under CC BY 4.0, combined and edited to show valve seat
It’s usually a flat surface in gate and globe valves that touches the valve disc or plug to create the seal. On the other hand, ball and butterfly valves often have a seat with a rounded or cone shape to seal against the ball or disc. Check valves might also have a seat powered by a spring to prevent backflow. The valve seats can be made from various materials like metal alloys, rubber, or plastics.
Valve Stem—the Pivotal Link
The valve stem design depends on the disc. For a ball valve, the stem is connected to a ball-shaped disc, which rotates to control the flow of fluids. In gate valves, the stem moves up and down to operate a gate-like disc.
Gate valve, licensed under CC BY 4.0
In butterfly valves, the stem is connected to a disc that rotates 90 degrees to regulate the flow. The valve stem design lets the operator control the movement of the disc, whether its linear or rotational. This gives them precise control over the fluid flow, making the stem a crucial part of a valve. The manual valve design has a handwheel or lever attached to the stem. Most household valves are this type and require the operator to physically turn the stem. Industrial valves often use electric or pneumatic actuators to move it remotely and automatically, which is essential in precision valve applications.
Make It Leak Free with Stem Packing
Valve stem packing, sometimes called packing gland, helps avoid leaks by creating a tight seal. There are a few common materials used, like graphite and PTFE. Both types of packing sometimes look like braided rope or cord and come in long spools. They are differentiated by color: graphite is often black, while PTFE is white or off-white. Graphite packing, made of braided graphite fibers, is ideal for high-temperature use and has good chemical resistance and durability. PTFE packing, made of synthetic material with low friction properties, ensures a great seal in both high and low temperatures. Most valves use stem packing as it is essential for the stem to be able to move while not leaking.
There’s Much, Much More to Learn!
We’ve looked into a few details of valve components and design, focusing on key parts like the valve body, bonnet, and trim. Knowing how these parts of a valve work is crucial for anyone working with fluid control systems or creating new designs, and we only scratched the surface here. Some valves, like check valves, have a different design, but that is outside the scope of this discussion. We’ve also included a few new innovations. Valve design and parts are always improving, offering fresh solutions to longstanding industry issues. It’s important for us to stay in the loop and adapt to these changes because they can help us work more efficiently, save money, and improve safety.
The science and tech that goes into valves is pretty impressive. Every part, from the body and bonnet to the trim of the valve, plays a big role in how it works. And the best part is, with new innovations on the horizon, the future of valve design has some exciting potential to make industry standards and practices even better.