What are the Structure Types and Advantages of Floating Ball Valve
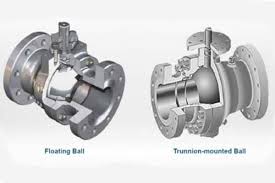
At present, there are many ball valve structures and specifications in our market, and new products and structures are emerging. The ball valve for sale can be divided into many types according to its main characteristics and applications.
The specific support mode of ball valve structure can lead to obvious change of ball valve structure, which directly affects the performance and use. When designing a ball valve, we usually determine the support mode of ball valve structure according to the requirements, fluid pressure, diameter and working temperature, and then a more suitable sealing structure can be selected.
motorized valve
Feature of Floating Ball Valve
The main feature of floating ball valve is that the ball has no supporting shaft, and the ball is mainly supported by the valve seat between the inlet ends and outlet ends of the valve. Moreover, the valve rod and the ball are movably connected, so the ball of this ball valve structure is mainly clamped between the two seats and presents a “floating” state. The ball can be directly driven by the handle or other driving devices through the valve rod, and can rotate between two valve seats.
Main Advantages of Floating Ball Valve
The main advantages of the floating ball valve that is widely used are simple structure, low cost, convenient manufacturing, safe and reliable work, so it has been widely used in various fields. Moreover, the sealing performance of the floating ball valve structure is directly related to the fluid pressure. Under the same conditions, generally speaking, the higher the pressure is, the easier it is to be sealed. The converse is also true. However, we should consider whether the material of the valve seat can withstand the load transmitted by the housing. The main force generated by the pressure of the fluid on the ball structure will all be transmitted to the valve seat.
In addition, for the floating ball valve of a relatively large diameter, when the pressure is high, the operating torque will increase, and the weight of the ball is also relatively large. It will cause that the direct distribution of the pressure generated by the self-weight on the sealing surface of the valve seat is relatively uneven. Generally speaking, the upper half-circle of the horizontal plane along the diameter of the channel is smaller and the lower half-circle is larger, which will directly lead to uneven wear of the valve seat and finally cause leakage.
Finally, we must apply a certain preload between the ball and the base so that the floating ball valve structure can also have good sealing performance under low working environment pressure. If the preload is insufficient, the sealing of the material can not be guaranteed. However, if the preload is too large, the friction torque between the ball structure and the valve seat will also increase, which may directly lead to irreversible plastic deformation between the valve seat materials and destroy the sealing performance.