Severe Service Valves
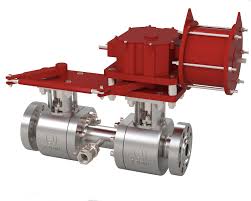
The Application of Severe Service Valves
Severe service valves are critical components in industries where extreme conditions challenge traditional valve performance. Severe service control valves, severe service ball valves, and severe service valves are designed to withstand high pressures, corrosive fluids, and abrasive materials. As a leading brand in valve solutions, Cameron specializes in engineering robust severe service valves tailored to meet demanding operational requirements. These valves ensure optimal control and reliability in applications such as chemical processing, power generation, oil and gas production, and refining. Cameron’s innovative designs prioritize safety, efficiency, and longevity, making them indispensable assets in harsh environments. From controlling flow rates to regulating pressure, severe service valves play a pivotal role in maximizing productivity and minimizing downtime in critical industrial processes.
grove ball valve
float ball valve
What Are The Types Of Severe Service Valves?
- Severe Service Control Valves: These valves are engineered to provide precise control over flow rates, pressure, and temperature in harsh environments. They feature robust construction and specialized trim materials to resist erosion, corrosion, and high temperatures.
- Severe Service Ball Valves: These valves utilize a spherical closure mechanism to regulate flow in severe applications. They offer tight shut-off capabilities and are resistant to abrasive media, high pressures, and corrosive fluids.
- Severe Service Globe Valves: Globe valves are widely used in severe service applications due to their excellent throttling capabilities and precise control over flow. They are designed to handle high-pressure drops, cavitation, and flashing conditions.
- Severe Service Butterfly Valves: Butterfly valves are preferred for their lightweight design and quick operation. In severe service applications, they are equipped with special coatings and trim materials to withstand erosive, abrasive, and corrosive fluids.
- Severe Service Check Valves: Check valves prevent reverse flow in pipelines and systems. In severe service environments, they are constructed with durable materials and designs to ensure reliable operation and tight sealing.
What Is Severe Service Valves?
Severe service valves are specialized components engineered to withstand extreme conditions such as high pressures, corrosive fluids, and abrasive materials. They are crucial in industries like chemical processing, power generation, oil and gas, where standard valves may fail. These valves, including severe service control valves and severe service ball valves, are designed with robust materials and configurations to ensure reliable performance and longevity in harsh environments, contributing to operational efficiency and safety.
How to Select the Right Severe Service Valves?
Selecting the right severe service valves requires considering factors like operating conditions, fluid characteristics, and industry regulations. Evaluate parameters such as pressure ratings, temperature range, corrosion resistance, and flow capacity to ensure compatibility with your application. Consult with experienced engineers and suppliers to identify the most suitable severe service valve that meets your specific requirements and ensures optimal performance and reliability.
Features of Severe Service Valves
- Robust Construction:
- Severe service valves feature robust construction using durable materials such as stainless steel or corrosion-resistant alloys.
- This ensures structural integrity and longevity, even in harsh operating conditions with high pressures and temperatures.
- Specialized Trim Materials:
- These valves incorporate specialized trim materials like stellite or tungsten carbide to resist erosion and corrosion caused by abrasive fluids.
- The use of advanced trim materials enhances valve performance and extends service life.
- High Pressure Rating:
- Severe service valves are designed with a high pressure rating to withstand extreme pressure fluctuations and maintain tight shut-off capabilities.
- This feature ensures reliable operation and minimizes the risk of leaks or valve failure.
- Throttling Capability:
- Many severe service valves offer precise throttling capability, allowing for accurate control of flow rates and pressure levels.
- This feature is essential in applications where precise flow control is critical for operational efficiency and safety.
- Cavitation and Erosion Resistance:
- Severe service valves are engineered to resist cavitation and erosion, common challenges in high-velocity flow applications.
- Advanced designs and specialized coatings mitigate the effects of cavitation and erosion, preserving valve performance over time.
Advantages and Disadvantages of Severe Service Valves
Advantages:
- Enhanced Durability:
- Severe service valves are built with robust materials and designs, ensuring longevity and reliability even in challenging environments.
- Improved Performance:
- These valves offer precise control over flow rates and pressure levels, contributing to enhanced process efficiency and operational control.
- Resistance to Harsh Conditions:
- Severe service valves withstand extreme pressures, temperatures, and corrosive fluids, making them suitable for demanding industrial applications.
- Reduced Downtime:
- Their durability and reliability minimize maintenance requirements and unplanned shutdowns, leading to increased uptime and productivity.
Disadvantages:
- Higher Initial Cost:
- Severe service valves typically come with a higher upfront investment compared to standard valves due to their specialized construction and materials.
- Complexity:
- Their advanced designs and features may require additional expertise for installation, operation, and maintenance, leading to increased complexity.
- Limited Availability:
- Severe service valves may have limited availability compared to standard valves, requiring longer lead times for procurement and replacement.
- Potential Over-specification:
- In some cases, using severe service valves in applications where they are not truly necessary may lead to over-specification and unnecessary costs.
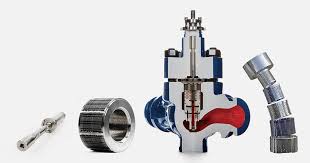
The Specifications of Severe Service Valves
Specification | Details |
---|---|
Type | Ball Valve |
Ball Material | Stainless Steel |
Attachment Type | Threaded |
Thread Standard | NPT (National Pipe Thread) |
Thread Size | 1/2 inch |
Body Material | Brass |
Safe for Use With | Water, Oil, Gas |
Handle Type | Lever |
Handle Material | Zinc Alloy |
Maximum Working Pressure (psi) | 600 |
Maximum Working Pressure (bar) | 41.4 |
Operating Pressure | 0 – 400 psi |
The Installation Steps for Severe Service Valves
- Preparation:
- Gather all necessary tools and equipment, including wrenches, pipe thread sealant, and a pipe cutter.
- Ensure the work area is clean and free from debris to prevent contamination during installation.
- Valve Inspection:
- Inspect the severe service valve for any damage or defects before installation, including cracks, dents, or corrosion.
- Verify that the valve’s specifications match the requirements of the application.
- Valve Positioning:
- Determine the optimal location for installing the valve within the pipeline system, considering factors such as accessibility and flow direction.
- Pipe Preparation:
- Cut the pipeline to the appropriate length using a pipe cutter, ensuring clean, square cuts to prevent leaks.
- Deburr the pipe ends to remove any sharp edges or burrs that could damage the valve or interfere with sealing.
- Valve Installation:
- Apply pipe thread sealant to the male threads of the valve and pipe fittings to ensure a tight seal.
- Thread the valve onto the pipeline by hand, ensuring proper alignment and engagement of the threads.
- Use wrenches to tighten the valve securely, taking care not to over-tighten and damage the threads or valve body.
- Pressure Testing:
- Conduct a pressure test on the installed valve to ensure there are no leaks or defects.
- Gradually increase the pressure to the maximum operating pressure specified for the valve and monitor for any signs of leakage.
- Final Inspection:
- Once the pressure test is successful, visually inspect the installed valve and surrounding area for any signs of leaks or abnormalities.
- Confirm that the valve operates smoothly and is positioned correctly within the pipeline system.
The Operation Theory of Severe Service Valves
- Robust Construction:
- Severe service valves are built with robust materials and construction techniques to withstand extreme pressures, temperatures, and fluid conditions. This includes the use of corrosion-resistant alloys, hardened trim materials, and reinforced valve bodies.
- Flow Control Mechanism:
- These valves employ various flow control mechanisms, such as ball, globe, butterfly, or check valves, depending on the application requirements. The choice of mechanism influences the valve’s ability to regulate flow rates, pressure drops, and fluid direction.
- Trim Design:
- The trim design of severe service valves plays a critical role in their operation. Trim components, such as the valve disc, seat, and stem, are engineered to resist erosion, corrosion, and abrasion caused by harsh fluids, including slurry and corrosive chemicals.
- Sealing Mechanism:
- Severe service valves incorporate advanced sealing mechanisms to ensure tight shut-off and prevent leakage under high-pressure conditions. This includes resilient seals, metal-to-metal seals, and specially designed packing arrangements to maintain sealing integrity.
- Actuation Options:
- Depending on the application requirements, severe service valves may be manually operated or equipped with actuation mechanisms such as pneumatic, hydraulic, or electric actuators. Actuators provide remote control and automation capabilities, enhancing operational efficiency and safety.
- Flow Characteristics:
- Severe service valves are designed to provide specific flow characteristics tailored to the application needs. This includes options for linear, equal percentage, or quick-opening flow profiles to optimize process performance and control.
- Maintenance Considerations:
- Proper maintenance is essential for ensuring the long-term performance of severe service valves. This includes regular inspection, lubrication, and replacement of worn components to prevent degradation and ensure reliable operation in severe environments.
The Parameters Chart of Severe Service Valves
Parameter | Description | Material |
---|---|---|
Valve Type | Type of valve (e.g., ball, globe, butterfly) | Varies based on valve type |
Body Material | Material of the valve body | Stainless Steel, Carbon Steel, Alloy Steel, Brass, Cast Iron, etc. |
Trim Material | Material of trim components (e.g., disc, seat, stem) | Stainless Steel, Alloy Steel, Hastelloy, Tungsten Carbide, Ceramic, etc. |
Sealing Mechanism | Mechanism for achieving tight shut-off | Resilient Seals, Metal-to-Metal Seals, PTFE (Teflon) Seals, etc. |
Actuation Type | Type of actuation mechanism (e.g., manual, pneumatic, electric) | Varies based on actuation type |
Pressure Rating | Maximum allowable pressure | Depends on valve design and specifications |
Temperature Rating | Maximum allowable temperature | Depends on valve design and specifications |
Flow Characteristic | Profile of flow through the valve (e.g., linear, equal percentage) | Depends on valve design and trim configuration |
Connection Type | Type of connection for installation (e.g., threaded, flanged) | Varies based on application requirements |
Size Range | Range of valve sizes available | Varies based on manufacturer and model |