What is a control valve?
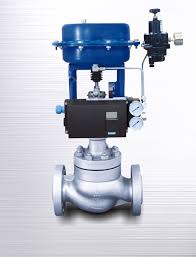
The Application of control valve
Cameron, a leading provider of flow and pressure control solutions, offers a diverse range of control valves to meet the demands of various industries. From hydraulic control valves for precision fluid management to hydraulic flow control valves for regulating volumetric flow rates, Cameron’s products cater to a wide array of applications. Additionally, the company’s camshaft oil control valves play a crucial role in optimizing engine performance and efficiency. Whether you require precise pressure regulation, accurate flow control, or specialized valve solutions, Cameron’s comprehensive portfolio ensures that you can find the right control valve to fit your specific needs.
air release valve for water line
What Are The Types Of control valve?
Globe Valves: These valves use a linear motion to throttle the flow by varying the size of the flow orifice, providing precise control over the fluid passage.
Ball Valves: Featuring a rotary ball mechanism, these valves offer excellent flow control capabilities with a simple quarter-turn operation, making them suitable for a wide range of applications.
Butterfly Valves: Designed with a disc-shaped obstruction that rotates into the flow path, butterfly valves provide efficient flow regulation and are commonly used in large-scale systems.
Diaphragm Valves: Utilizing a flexible diaphragm to restrict or allow flow, these valves are particularly well-suited for handling corrosive or viscous fluids.
Pressure Reducing Valves: These valves automatically reduce and maintain a lower downstream pressure, regardless of changes in upstream pressure, ensuring consistent system performance.
Pressure Relief Valves: Engineered to open and release excess pressure when the system pressure exceeds a pre-set limit, these valves protect equipment from damage.
What Is control valve?
A control valve is a critical component in fluid and gas handling systems that regulates the flow, pressure, or other parameters of the medium being transported. These valves play a vital role in maintaining system performance, ensuring safety, and optimizing process efficiency. Control valves accomplish this by modulating the opening or closing of a flow path, allowing the operator or automated system to precisely manage the desired variable, such as flow rate, pressure, or liquid level. Leveraging advanced actuators and intelligent control algorithms, Cameron’s control valve offerings provide reliable and responsive operation, making them an essential part of a wide range of industrial, commercial, and infrastructure applications.
How to Select the Right control valve?
When selecting the appropriate control valve for an application, several key factors must be considered. For pressure control valves, parameters such as the required pressure range, flow capacity, and response time are crucial. The valve material and end connections must also be compatible with the system’s operating conditions and media. In the case of flow control valves, factors like the required flow rate, pressure drop, and rangeability should guide the selection process. Additionally, the valve’s size, actuation method, and compatibility with the piping system are important considerations. Careful evaluation of these criteria, coupled with a thorough understanding of the application’s needs, will ensure the selection of the most suitable valve solution from Cameron’s comprehensive product portfolio.
Features of control valve
Pressure Capability: Control valves are designed to handle a wide range of pressure requirements, from low-pressure domestic applications to high-pressure industrial processes.
Flow Regulation: The flow control capabilities of these valves enable precise management of volumetric flow rates, ensuring optimal process efficiency and product quality.
Actuation: Control valves can be manually operated or equipped with automated actuators, such as electric or pneumatic, to allow for remote operation and seamless integration into process control systems.
Material Compatibility: The selection of valve materials is critical to ensure compatibility with the fluid media, operating temperatures, and corrosive environments encountered in the system.
Response Time: Rapid response times are essential for control valves in applications where fast pressure or flow adjustments are required, such as in compressor systems or high-speed processes.
Reliability: Robust construction and stringent quality control measures ensure the long-term reliability and durability of Cameron’s control valve solutions, minimizing downtime and maintenance costs.
Advantages and Disadvantages of control valve
Advantages of Control Valves:
- Precision Control: Control valves allow for accurate regulation of flow, pressure, and other process variables, enabling fine-tuned management of system performance.
- Improved Efficiency: By optimizing the flow and pressure within a system, control valves can contribute to increased energy efficiency and reduced operating costs.
- Enhanced Safety: The ability to rapidly respond to changes in system conditions and automatically regulate critical parameters helps control valves enhance the overall safety of the process.
- Versatility: Control valves can be tailored to a wide range of applications, from industrial processes to commercial and residential systems, making them a versatile solution.
Disadvantages of Control Valves:
- Complexity: The intricate design and integration of control valves can increase the complexity of the overall system, requiring specialized knowledge for installation and maintenance.
- Potential Failure Points: As moving parts, control valves are susceptible to wear and tear over time, which can lead to potential failures if not properly maintained.
- Higher Initial Costs: The advanced features and precision engineering of control valves typically result in higher initial acquisition costs compared to simpler valve solutions.
- Power Requirements: Certain control valves, such as those with electric or pneumatic actuators, require a continuous power supply to operate, which can add to the overall system energy consumption.
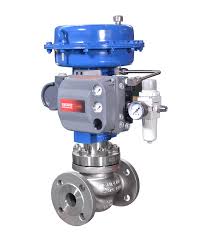
The Specifications of control valve
Specification | Details |
---|---|
Type | Ball Valve |
Ball Material | Stainless Steel |
Attachment Type | Threaded |
Thread Standard | NPT |
Thread Size | 1/2 inch |
Body Material | Carbon Steel |
Safe for Use With | Water, Oil, Air, Gas |
Handle Type | Lever |
Handle Material | Stainless Steel |
Maximum Working Pressure (psi) | 1000 |
Maximum Working Pressure (bar) | 69 |
Operating Pressure | 50-800 psi (3.4-55.2 bar) |
The Installation Steps for control valve
Step 1: Prepare the Piping System
- Ensure the piping is properly aligned and supported to avoid any strain on the valve.
- Verify the pipe size matches the valve’s connections.
- Clean the pipe interior to remove any debris or contamination.
Step 2: Position the Valve
- Orientate the valve in the correct flow direction, typically indicated by arrows on the valve body.
- Allow sufficient clearance around the valve for easy access and maintenance.
Step 3: Connect the Valve to the Piping
- For threaded connections, apply thread sealant and tighten the valve into the pipe using a wrench.
- For flanged connections, align the valve’s flange holes with the pipe flanges, insert the bolts, and tighten them in a star or crisscross pattern.
Step 4: Install the Valve Actuator (if applicable)
- Mount the pneumatic, electric, or manual actuator securely to the valve’s stem.
- Connect the actuator to the control system or power source as per the manufacturer’s instructions.
Step 5: Perform a Leak Test
- Pressurize the system and check for any leaks around the valve’s connections.
- Tighten the fittings or make adjustments as necessary to ensure a tight seal.
Step 6: Commission the Valve
- Cycle the valve through its full range of motion to ensure smooth and responsive operation.
- Calibrate the valve’s control parameters to match the system requirements.
The Operation Theory of control valve
Pressure Control Valves:
Pressure control valves operate by modulating the flow of a fluid or gas to maintain a desired pressure setpoint. They use a combination of a sensing element, a control mechanism, and an actuator to continuously monitor the pressure and adjust the valve opening accordingly. This allows the valve to respond to changes in the system and keep the pressure within the desired range.
Modulating Control Valves:
Modulating control valves are a type of control valve that can continuously adjust their position to regulate the flow or pressure. Unlike on-off valves, modulating valves can operate across a wide range of positions, enabling precise control and fine-tuning of the process variable. They are commonly used in applications that require accurate and responsive flow or pressure management.
Gas Control Valves:
Gas control valves are designed to regulate the flow and pressure of gaseous media, such as natural gas, air, or industrial gases. These valves incorporate features to handle the specific challenges of gas systems, including the ability to withstand high pressures, minimize leakage, and provide reliable, repeatable performance. The operation of gas control valves relies on the principles of fluid dynamics and the valve’s ability to modulate the gas flow in response to changing system conditions.