Floating Ball Valve

The Application of Floating Ball Valve
The Floating Ball Valve is a crucial component in fluid control systems, trusted for its reliability and versatility. This valve, exemplified by industry leaders like Barton 200AS, ITT Barton 288C, and Barton 450C, offers precise flow control and tight shut-off, ensuring efficient operation in various applications. Rotork Gear Valve and Cameron Gear Valve are among the top choices for professionals seeking dependable fluid control solutions. Whether in oil and gas, petrochemical, or industrial processes, the Floating Ball Valve provides essential functionality, making it indispensable in modern engineering.
cooling tower valves companies
cooling tower valve company
What Is Floating Ball Valve?
A Floating Ball Valve is a type of quarter-turn valve used to control the flow of fluid in pipelines. It features a floating ball design, where the ball is not fixed in place but instead floats between two seats, one upstream and one downstream. When the valve is open, the pressure of the fluid pushes the ball towards the downstream seat, creating a tight seal and preventing leakage. When closed, the ball rotates perpendicular to the flow direction, blocking the flow of fluid. Floating Ball Valves are commonly used in various industries for their reliability, ease of maintenance, and versatility in controlling fluid flow.
Disadvantages of Floating Ball Valves
- Relies solely on downstream seating for medium loads.
- Challenges in operation under high upstream pressure.
- Seating directly bears ball’s weight, limiting pressure capacity.
The Specifications of Floating Ball Valve
Specification | Details |
---|---|
Type | Floating Ball Valve |
Ball Material | Stainless Steel, Carbon Steel, Alloy Steel |
Attachment Type | Flanged, Threaded, Welded |
Thread Standard | ASME B1.20.1, ISO 7/1, BS 21, DIN 2999, etc. |
Thread Size | 1/2″ – 10″ (DN15 – DN250) |
Body Material | Carbon Steel, Stainless Steel, Alloy Steel |
Safe for Use With | Liquids, Gases, Steam |
Handle Type | Lever, Gear, Electric, Pneumatic |
Handle Material | Carbon Steel, Stainless Steel, Alloy Steel |
Maximum Working Pressure psi | Up to 3000 psi |
Maximum Working Pressure bar | Up to 207 bar |
Operating Pressure | Based on valve rating and application requirements |
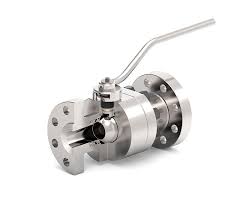
The Parameter of Floating Ball Valve
- Type: Gear Operated Ball Valve
- Ball Material: Stainless Steel, Carbon Steel, Alloy Steel
- Attachment Type: Flanged, Threaded, Welded
- Thread Standard: ASME B1.20.1, ISO 7/1, BS 21, DIN 2999, etc.
- Thread Size: 1/2″ – 10″ (DN15 – DN250)
- Body Material: Carbon Steel, Stainless Steel, Alloy Steel
- Safe for Use With: Liquids, Gases, Steam
- Handle Type: Gear
- Handle Material: Carbon Steel, Stainless Steel, Alloy Steel
- Maximum Working Pressure psi: Up to 3000 psi
- Maximum Working Pressure bar: Up to 207 bar
- Operating Pressure: Based on valve rating and application requirements
The Operation Theory of Floating Ball Valve
The operation theory of the Floating Ball Valve involves a floating ball design, ensuring reliable sealing. In a ZECO Valve like Barton 316C and Barton 224C, the ball is free to move between two seats. When the valve is open, the fluid pressure pushes the ball towards the downstream seat, sealing the valve. When closed, the ball rotates perpendicular to the flow, blocking it. This design ensures tight shut-off and prevents leakage in various fluid control applications.
The Parameters Table of Floating Ball Valve
Component | Material |
---|---|
Body | Carbon Steel, Stainless Steel, Alloy Steel |
Ball | Stainless Steel, Carbon Steel |
Stem | Stainless Steel |
Seat | PTFE, RPTFE, Nylon, Peek, etc. |
Gasket | PTFE, Graphite, etc. |
Bolting | Stainless Steel, Alloy Steel |
Handle | Carbon Steel, Stainless Steel, Alloy Steel |