Which Valves Are Ideal For Slurry Applications?
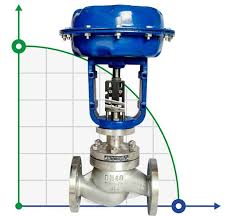
The Application of Slurry Valves
Cameron, a renowned industrial solutions provider, offers high-quality slurry valves designed for various applications. These valves, including slurry safety valves, slurry ball valve designs, and slurry check valves, are specifically engineered to handle abrasive and corrosive slurries efficiently. With robust construction and specialized materials, they ensure reliable performance and longevity in demanding environments. Slurry safety valves prioritize safety by preventing overpressure incidents, safeguarding equipment and personnel. Slurry ball valve designs provide precise control over slurry flow, enhancing operational efficiency and reducing downtime. Slurry check valves offer reliable one-way flow control, preventing backflow and maintaining system integrity. Cameron’s commitment to innovation and quality ensures that its slurry valves meet the rigorous demands of industries such as mining, wastewater treatment, and chemical processing, providing reliable solutions for challenging slurry applications.
Which Valves Are Ideal For Slurry Applications?
Valves ideal for slurry applications typically include slurry valves specifically designed to handle abrasive and corrosive slurries efficiently. Among these, slurry ball valves, slurry check valves, and slurry knife gate valves are commonly preferred due to their ability to withstand the harsh conditions of slurry systems. These valves feature robust construction, specialized materials, and designs tailored to prevent clogging and erosion caused by abrasive particles in the slurry. Additionally, slurry pinch valves and slurry diaphragm valves offer effective flow control and sealing capabilities, making them suitable for various slurry handling tasks. Ultimately, the choice of valve depends on the specific requirements of the slurry application, including flow rate, pressure, and composition of the slurry.
What Are The Types Of Slurry Valves?
- Slurry Ball Valves: These valves feature a spherical closure element (ball) that rotates to control flow. They are well-suited for on/off applications and provide excellent sealing even in abrasive slurry environments.
- Slurry Check Valves: Also known as non-return or one-way valves, slurry check valves allow flow in one direction and prevent backflow. They are essential for maintaining system integrity and preventing reverse flow of abrasive slurries.
- Slurry Knife Gate Valves: These valves feature a sharp-edged gate that slides across the flow path to control flow. They are specifically designed to handle thick, abrasive slurries and are often used in applications where frequent clogging is a concern.
- Slurry Pinch Valves: These valves use a flexible sleeve or pinch mechanism to control flow by compressing or releasing the sleeve. They offer excellent abrasion resistance and are suitable for handling highly abrasive slurries.
- Slurry Diaphragm Valves: Similar to pinch valves, slurry diaphragm valves use a flexible diaphragm to control flow. They provide precise throttling and sealing capabilities, making them ideal for slurry applications requiring accurate flow control.
What Is Slurry Valves?
Slurry valves are specialized valves designed to handle abrasive and corrosive slurries in various industrial applications. These valves are constructed with materials and designs specifically tailored to withstand the harsh conditions of slurry systems, which often contain solid particles suspended in liquid. Slurry valves are engineered to provide reliable performance, tight sealing, and resistance to erosion and abrasion caused by the abrasive particles present in the slurry. They play a crucial role in industries such as mining, mineral processing, wastewater treatment, and chemical processing, where the handling of slurries is common. Slurry valves are available in different types, including ball valves, check valves, knife gate valves, pinch valves, and diaphragm valves, each offering unique features suited to specific slurry handling requirements.
How Does Slurry Valves work?
Slurry valves work by utilizing specialized designs and materials to withstand the abrasive and corrosive nature of slurries. They employ mechanisms such as rotating balls, sliding gates, or flexible sleeves to control the flow of the slurry. These valves ensure tight sealing to prevent leakage and maintain system integrity, even in harsh slurry environments. The robust construction of slurry valves enables them to resist erosion and abrasion caused by solid particles suspended in the slurry, ensuring long-term reliability and performance.
Features of Slurry Valves
- Abrasion Resistance: Designed with materials such as abrasion-resistant alloys or ceramics to withstand the erosive effects of abrasive slurries.
- Tight Sealing: Incorporate specialized seals and gaskets to ensure tight sealing, preventing leakage and maintaining system integrity.
- Robust Construction: Feature sturdy construction and reinforced components to withstand the high pressures and impact forces associated with slurry applications.
- Erosion Prevention: Utilize flow control mechanisms such as ball valves or knife gate valves to minimize erosion of valve components by directing the flow of the slurry.
- Clog Resistance: Engineered with self-cleaning or non-clogging designs to prevent blockages caused by solid particles in the slurry.
- Corrosion Resistance: Constructed with corrosion-resistant materials such as stainless steel or high-performance alloys to withstand the corrosive nature of slurries.
- Versatility: Offer a range of valve types, including ball valves, check valves, knife gate valves, and pinch valves, to suit different slurry handling requirements.
- Ease of Maintenance: Designed for easy maintenance and repair, with accessible components and minimal downtime for servicing.
Advantages of Slurry Valves
- Abrasion Resistance: Built to withstand the erosive effects of abrasive slurries, ensuring long-term durability and reliability.
- Tight Sealing: Ensure tight sealing to prevent leakage and maintain system integrity, even in harsh slurry environments.
- Robust Construction: Feature sturdy construction and reinforced components to withstand high pressures and impact forces associated with slurry applications.
- Efficient Flow Control: Provide precise control over the flow of slurries, allowing for accurate regulation and management of processes.
- Reduced Maintenance: Designed with self-cleaning or non-clogging mechanisms to minimize downtime and maintenance costs associated with blockages.
- Corrosion Resistance: Constructed with corrosion-resistant materials to withstand the corrosive nature of slurries, enhancing longevity and performance.
- Versatility: Offer a variety of valve types to suit different slurry handling requirements, ensuring flexibility and adaptability.
- Safety: Enhance safety by preventing overpressure incidents and maintaining system stability, safeguarding equipment and personnel.
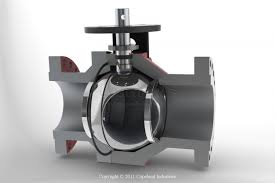
The Specifications of Slurry Valves
Specification | Details |
---|---|
Type | Slurry Valve |
Ball Material | Stainless Steel, Alloy Steel, Ceramic |
Attachment Type | Flanged, Threaded |
Thread Standard | ASME B1.20.1, DIN, ISO |
Thread Size | 1/2 inch to 24 inches (for threaded), 2 inches to 48 inches (for flanged) |
Body Material | Ductile Iron, Cast Steel, Stainless Steel, Carbon Steel |
Safe for Use With | Abrasive slurries, Corrosive chemicals, High-viscosity fluids |
Handle Type | Handwheel, Gear Operator, Actuator |
Handle Material | Stainless Steel, Aluminum Alloy, Plastic |
Maximum Working Pressure (psi) | Up to 1500 psi |
Maximum Working Pressure (bar) | Up to 103.4 bar |
Operating Pressure | 10 psi to 1500 psi (0.7 bar to 103.4 bar) |
The Parameter of Slurry Valves
- Type: Slurry Valve
- Ball Material Options: Stainless Steel, Alloy Steel, Ceramic
- Attachment Types Available: Flanged, Threaded
- Thread Standard: ASME B1.20.1, DIN, ISO
- Thread Size Range: 1/2 inch to 24 inches (for threaded), 2 inches to 48 inches (for flanged)
- Body Material Choices: Ductile Iron, Cast Steel, Stainless Steel, Carbon Steel
- Safe for Use With: Abrasive slurries, Corrosive chemicals, High-viscosity fluids
- Handle Types: Handwheel, Gear Operator, Actuator
- Handle Material Options: Stainless Steel, Aluminum Alloy, Plastic
- Maximum Working Pressure (psi): Up to 1500 psi
- Maximum Working Pressure (bar): Up to 103.4 bar
- Operating Pressure Range: From 10 psi to 1500 psi (0.7 bar to 103.4 bar)
The Operation Theory of Slurry Valves
The operation theory of slurry valves, including slurry ball valves and slurry control valves, revolves around their ability to effectively manage the flow of abrasive and corrosive slurries in industrial applications.
In slurry ball valves, a spherical closure element (ball) within the valve body controls the flow of the slurry. When the valve is open, the ball rotates to allow the passage of the slurry, while in the closed position, it forms a tight seal against the valve seat to prevent leakage.
Similarly, slurry control valves employ various mechanisms such as diaphragms, sleeves, or gates to regulate the flow of the slurry. These mechanisms are designed to withstand the abrasive nature of slurries and provide precise control over flow rates and pressures.
The Parameters Table of Slurry Valves
Parameter | Details |
---|---|
Type | Slurry Valve |
Ball Material Options | Stainless Steel, Alloy Steel, Ceramic |
Stem Material Options | Stainless Steel, Alloy Steel, Ceramic |
Seat Material Options | PTFE (Teflon), EPDM, NBR (Nitrile), Ceramic |
Body Material Options | Ductile Iron, Cast Steel, Stainless Steel, Carbon Steel |
Bonnet Material Options | Ductile Iron, Cast Steel, Stainless Steel, Carbon Steel |
Seal Material Options | EPDM, NBR (Nitrile), Viton, Ceramic |
Handle Material Options | Stainless Steel, Aluminum Alloy, Plastic |
Bolting Material Options | Stainless Steel, Carbon Steel, Alloy Steel |
Flange Material Options | Carbon Steel, Stainless Steel, Alloy Steel |
Operating Mechanism | Manual (Handwheel), Gear Operator, Actuator |
Operating Temperature | -30°C to 200°C (-22°F to 392°F) |
Maximum Working Pressure | Up to 1500 psi (103.4 bar) |