Overview of Valve Bonnets: Crucial Parts of Industrial Valves
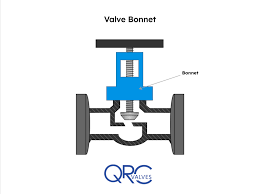
The Application of Valve Bonnets
Cameron, a leading industrial solutions provider, offers a wide range of valve bonnets tailored for various applications. From pressure seal bonnet check valves to integral bonnet needle valves, these components play critical roles in ensuring the integrity and efficiency of valve systems. The valve bonnet serves as a protective cover for the valve’s internal components, safeguarding them from environmental factors and maintaining optimal performance. In pressure-seal designs, the bonnet provides a secure seal under high-pressure conditions, crucial for applications in oil and gas, power generation, and chemical processing industries. Similarly, integral bonnet needle valves offer compact and reliable solutions for precision flow control in instrumentation and fluid handling systems. Cameron’s commitment to quality and innovation ensures that its valve bonnets meet the stringent demands of diverse industrial environments, providing reliable performance and longevity.
valve bonnet
valve bonnet types
parallel slide valve
bonnet on a valve
long bonnet ball valve
bonnet gate valve
What Are The Types Of Valve Bonnets?
- Bolted Bonnet: Consists of a separate bonnet bolted to the valve body, allowing for easy access to internal components for maintenance or repair.
- Pressure Seal Bonnet: Features a bonnet that is integrally forged with the valve body, providing a secure seal under high-pressure conditions, commonly used in high-pressure and high-temperature applications.
- Screwed Bonnet: Utilizes screw threads to secure the bonnet to the valve body, offering a simple and cost-effective design suitable for low-pressure applications.
- Welded Bonnet: Involves welding the bonnet to the valve body, ensuring a permanent seal and enhanced structural integrity, often used in critical or hazardous environments.
- Integral Bonnet Needle Valve: Integrates the bonnet with the valve body, providing compact and leak-tight solutions for precision flow control in instrumentation and fluid handling systems.
What Is Valve Bonnets?
Valve bonnets are protective covers or enclosures that are an integral part of valve assemblies. They serve to enclose the valve internals, including the stem, packing, and seating surfaces, providing protection from external elements and ensuring the integrity of the valve operation. Valve bonnets come in various designs such as bolted, pressure seal, screwed, or welded, depending on the type of valve and its intended application. They play a crucial role in maintaining the reliability and performance of valves in diverse industries ranging from oil and gas to power generation and chemical processing.
How Does Valve Bonnets work?
Valve bonnets function by enclosing and sealing the internal components of a valve, including the stem, packing, and seating surfaces. They create a protective barrier against external elements, such as dirt, debris, and corrosive substances, ensuring the integrity and longevity of the valve operation. Valve bonnets also facilitate access to the internal components for maintenance, repair, or adjustment, enhancing the efficiency and reliability of valve systems in various industrial applications.
Features of Valve Bonnets
- Protective Enclosure: Serve as a protective cover for the internal components of the valve, safeguarding them from external factors such as dirt, debris, and corrosive substances.
- Sealing Functionality: Provide a secure seal to prevent leakage and maintain pressure integrity within the valve system, ensuring safe and efficient operation.
- Accessibility: Allow easy access to the internal components of the valve for maintenance, repair, or adjustment, minimizing downtime and facilitating efficient servicing.
- Variety of Designs: Available in various designs such as bolted, pressure seal, screwed, or welded, catering to different valve types and operating conditions.
- Pressure Rating: Offer different pressure ratings to accommodate a wide range of applications, from low-pressure to high-pressure environments.
- Temperature Resistance: Constructed from materials capable of withstanding high temperatures, ensuring reliability and longevity in extreme operating conditions.
- Corrosion Resistance: Designed with corrosion-resistant materials to withstand the effects of corrosive substances, prolonging the lifespan of the valve bonnet and the overall valve assembly.
Advantages of Valve Bonnets
- Protection: Provide a protective covering for the internal components of the valve, safeguarding them from external elements such as dirt, debris, and corrosive substances.
- Leak Prevention: Ensure a secure seal to prevent leakage and maintain pressure integrity within the valve system, enhancing safety and efficiency.
- Accessibility: Facilitate easy access to internal components for maintenance, repair, or adjustment, reducing downtime and improving operational efficiency.
- Versatility: Available in various designs and materials to suit different valve types and operating conditions, offering flexibility and adaptability.
- Durability: Constructed from robust materials capable of withstanding high temperatures and corrosive environments, ensuring long-term reliability and performance.
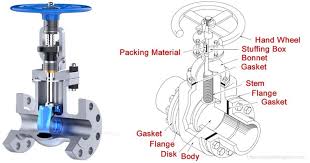
The Specifications of Valve Bonnets
Specification | Details |
---|---|
Type | Valve Bonnet |
Ball Material | Stainless Steel, Carbon Steel, Brass |
Attachment Type | Bolted, Pressure Seal, Screwed, Welded |
Thread Standard | ASME B1.20.1, DIN, ISO |
Thread Size | 1/2 inch to 2 inches (for threaded), 2 inches to 24 inches (for flanged) |
Body Material | Ductile Iron, Cast Steel, Stainless Steel, Carbon Steel |
Safe for Use With | Various fluids including water, oil, gas, chemicals |
Handle Type | Handwheel, Gear Operator, Actuator |
Handle Material | Stainless Steel, Aluminum Alloy, Plastic |
Maximum Working Pressure | Up to 2500 psi (172.4 bar) |
Operating Pressure | 10 psi to 2500 psi (0.7 bar to 172.4 bar) |
The Parameter of Valve Bonnets
- Type: Valve Bonnet
- Ball Material Options: Stainless Steel, Carbon Steel, Brass
- Attachment Types Available: Bolted, Pressure Seal, Screwed, Welded
- Thread Standard: ASME B1.20.1, DIN, ISO
- Thread Size Range: 1/2 inch to 2 inches (for threaded), 2 inches to 24 inches (for flanged)
- Body Material Choices: Ductile Iron, Cast Steel, Stainless Steel, Carbon Steel
- Safe for Use With: Various fluids including water, oil, gas, chemicals
- Handle Types: Handwheel, Gear Operator, Actuator
- Handle Material Options: Stainless Steel, Aluminum Alloy, Plastic
- Maximum Working Pressure (psi): Up to 2500 psi
- Maximum Working Pressure (bar): Up to 172.4 bar
- Operating Pressure Range: From 10 psi to 2500 psi (0.7 bar to 172.4 bar)
The Operation Theory of Valve Bonnets
The operation theory of valve bonnets, including those used in bolted bonnet ball valves and closed bonnet safety valves, revolves around their critical role in maintaining the integrity and functionality of valve assemblies.
In bolted bonnet ball valves, the bonnet is bolted to the valve body, creating a secure seal that prevents leakage and ensures pressure containment. This design allows for easy access to the valve internals for maintenance or repair, enhancing the versatility and longevity of the valve.
Closed bonnet safety valves employ a sealed bonnet design to prevent the release of hazardous fluids in case of overpressure situations. The closed bonnet ensures that the valve remains securely sealed until the pressure exceeds the set threshold, at which point it opens to relieve the excess pressure, safeguarding equipment and personnel.
The Parameters Table of Valve Bonnets
Parameter | Details |
---|---|
Type | Valve Bonnet |
Material Options | Stainless Steel, Carbon Steel, Brass, Ductile Iron |
Attachment Types | Bolted, Pressure Seal, Screwed, Welded |
Thread Standard | ASME B1.20.1, DIN, ISO |
Thread Size Range | 1/2 inch to 2 inches (for threaded), 2 inches to 24 inches (for flanged) |
Safe for Use With | Various fluids including water, oil, gas, chemicals |
Handle Types | Handwheel, Gear Operator, Actuator |
Handle Material Options | Stainless Steel, Aluminum Alloy, Plastic |