Automated Valves
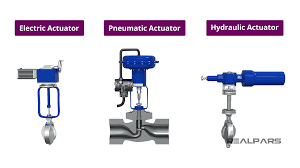
The Application of Automated Valves
Introducing Cameron’s cutting-edge automated ball valve technology, revolutionizing industrial operations worldwide. At our valve automation center, precision meets efficiency, offering tailored solutions for diverse applications. Our state-of-the-art valve automation system optimizes processes, enhancing safety and productivity.
What Are The Types Of Automated Valves?
- Automated Ball Valves: These valves use a spherical closure element to control flow. They are widely used for on/off and throttling applications.
- Automated Butterfly Valves: Butterfly valves have a disc mounted on a rotating shaft to control flow. They are often used for large flow applications and are quick to operate.
- Automated Globe Valves: Globe valves have a linear motion closing element, which provides precise flow control. They are commonly used in applications that require fine tuning of flow rates.
- Automated Gate Valves: Gate valves have a sliding gate to control flow. They are typically used in applications where a straight-line flow of fluid and minimum restriction is required.
- Automated Diaphragm Valves: Diaphragm valves use a flexible diaphragm to regulate flow. They are suitable for handling corrosive or abrasive fluids.
- Automated Plug Valves: Plug valves use a cylindrical or conically tapered plug to control flow. They are often used in applications requiring frequent operation and tight shutoff.
What Is Automated Valves?
Automated valves are mechanical devices designed to control the flow of fluids such as gases, liquids, or slurries in industrial processes. They incorporate automated mechanisms, such as actuators or motors, to open, close, or modulate the valve in response to signals from a control system. This automation reduces the need for manual intervention, improving efficiency, safety, and reliability in various industries, including oil and gas, chemical, water treatment, and manufacturing. Automated valves play a critical role in regulating fluid flow, pressure, and temperature, contributing to smoother operations and optimized processes.
How to Select the Right Automated Valves?
Selecting the right automated valves involves considering several factors such as the type of fluid, flow rate, pressure, temperature, and application requirements. Begin by assessing the specific needs of your process, including the desired level of automation, compatibility with existing systems, and regulatory compliance. Consult with experts to determine the most suitable valve type, size, material, and actuation method to ensure optimal performance and longevity in your operation. Additionally, prioritize features like reliability, maintenance requirements, and cost-effectiveness to make an informed decision that meets both current and future needs.
Features of Automated Valves
- Actuation: Automated valves offer various actuation methods such as electric, pneumatic, or hydraulic, providing flexibility in operation based on system requirements.
- Remote Control: They enable remote operation and monitoring, allowing adjustments to be made from a centralized location for enhanced efficiency and convenience.
- Position Feedback: Many automated valves incorporate position feedback mechanisms to provide real-time information on valve position, aiding in process control and troubleshooting.
- Fail-Safe Features: Some automated valves are equipped with fail-safe mechanisms that ensure they return to a predetermined position in the event of power failure or system malfunction, enhancing safety.
- Integration Capabilities: They can be seamlessly integrated into existing automation systems, facilitating interoperability and simplifying control and monitoring tasks.
- Diagnostic Tools: Advanced automated valves may include diagnostic features such as predictive maintenance alerts or condition monitoring, enabling proactive maintenance and minimizing downtime.
- Modularity: Modular designs allow for easy customization and scalability, accommodating evolving operational needs without requiring extensive system modifications.
- Environmental Adaptability: Automated valves are designed to withstand harsh environmental conditions, corrosion, and high temperatures, ensuring reliable performance in diverse applications.
Advantages and Disadvantages of Automated Valves
Advantages:
- Increased Efficiency: Automated valves streamline operations by reducing manual intervention, leading to improved efficiency and productivity.
- Enhanced Safety: They minimize human error and reduce the risk of accidents by providing precise control over fluid flow, pressure, and temperature.
- Remote Operation: Automated valves allow for remote monitoring and control, enabling operators to manage processes from a safe distance and respond quickly to changes or emergencies.
- Consistent Performance: They offer consistent and reliable performance, ensuring accurate and repeatable control over extended periods.
- Integration with Automation Systems: Automated valves seamlessly integrate with existing automation systems, enhancing overall system functionality and interoperability.
Disadvantages:
- Initial Cost: The initial investment in automated valves and associated control systems can be higher compared to manual valves, which may pose a barrier to adoption for some applications.
- Complexity: Automated valves require specialized knowledge for installation, programming, and maintenance, which can be a challenge for inexperienced operators or maintenance personnel.
- Dependency on Power: They rely on power sources for operation, making them susceptible to power outages or electrical failures that could disrupt processes.
- Potential for Malfunction: Like any mechanical or electronic device, automated valves can experience malfunctions or failures, requiring regular maintenance and monitoring to ensure proper functioning.
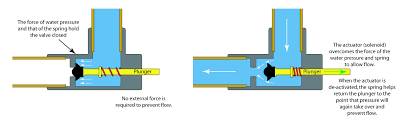
The Specifications of Automated Valves
Specification | Details |
---|---|
Type | Automated Ball Valve |
Ball Material | Stainless Steel |
Attachment Type | Flanged |
Thread Standard | N/A |
Thread Size | N/A |
Body Material | Carbon Steel |
Safe for Use With | Water, Oil, Gas |
Handle Type | Automated |
Handle Material | N/A |
Maximum Working Pressure (psi) | 1500 psi |
Maximum Working Pressure (bar) | 103.42 bar |
Operating Pressure | 0-500 psi |
The Installation Steps for Automated Valves
- Preparation:
- Ensure all necessary tools and equipment are available.
- Review installation instructions provided by the manufacturer.
- Location Selection:
- Identify the ideal location for the valve based on system requirements and accessibility.
- Valve Mounting:
- Securely mount the valve to the pipeline using appropriate bolts and gaskets.
- Align the valve properly to ensure smooth operation.
- Actuator Installation:
- Attach the actuator to the valve according to manufacturer specifications.
- Connect any necessary wiring or tubing for power and control signals.
- Power Connection:
- Connect the power source to the actuator following electrical safety guidelines.
- Ensure proper grounding to prevent electrical hazards.
- Control System Integration:
- Integrate the valve with the control system, if applicable, following wiring diagrams and protocols provided.
- Testing:
- Conduct a thorough functional test to ensure proper installation and operation.
- Verify valve movement, position feedback, and responsiveness to control signals.
- Calibration:
- Calibrate the valve and actuator as needed to achieve desired performance and accuracy.
- Adjust settings for pressure, flow, and other parameters as required.
- Documentation:
- Maintain detailed records of installation steps, test results, and calibration settings for future reference.
- Update system documentation and diagrams to reflect the new valve installation.
- Training:
- Provide training to relevant personnel on the operation, maintenance, and troubleshooting of the automated valve system.
The Operation Theory of Automated Valves
- Industrial Valve Automation:
- Industrial valve automation involves the integration of valves with automated systems to control the flow of fluids in industrial processes.
- It employs various actuation methods such as electric, pneumatic, or hydraulic actuators to manipulate valve positions based on input signals from control systems.
- Valve automation enhances efficiency, safety, and reliability by reducing manual intervention and enabling remote operation and monitoring.
- Automated Valves:
- Automated valves are mechanical devices designed to regulate fluid flow through pipelines, tanks, and other systems.
- They consist of a valve body and an actuator, which may be electric, pneumatic, or hydraulic, depending on the application.
- The actuator translates control signals from the automation system into mechanical motion, either opening, closing, or modulating the valve as needed.
- Automated valves may incorporate position feedback mechanisms to provide real-time information on valve position, ensuring precise control and enabling automated processes.
- Operation Theory:
- The operation theory of automated valves revolves around the seamless coordination between the actuator and the valve mechanism.
- When a control signal is received from the automation system, the actuator converts it into mechanical motion to adjust the valve position.
- Electric actuators use motors to drive gears or screws, while pneumatic actuators rely on compressed air to generate force and hydraulic actuators use hydraulic fluid pressure.
- The valve mechanism, typically consisting of a gate, ball, butterfly, or globe, then moves accordingly to regulate fluid flow.
- Position feedback sensors may send signals back to the automation system to confirm the valve’s position and ensure precise control.
The Parameters Chart of Automated Valves
Parameter | Material |
---|---|
Valve Body | Stainless Steel, Carbon Steel, Cast Iron, Brass, PVC, CPVC, Bronze, Alloy Steel, etc. |
Valve Seat | PTFE (Polytetrafluoroethylene), Metal (Stainless Steel, Brass, etc.), EPDM (Ethylene Propylene Diene Monomer), Viton, NBR (Nitrile Butadiene Rubber), etc. |
Valve Ball | Stainless Steel, Brass, PVC, CPVC, Alloy Steel, Ceramic, Titanium, etc. |
Valve Stem | Stainless Steel, Brass, Aluminum, Alloy Steel, Titanium, etc. |
Valve Actuator Housing | Aluminum, Cast Iron, Stainless Steel, Plastic (Polypropylene, PVC), etc. |
Actuator Type | Electric (with materials such as Aluminum, Stainless Steel), Pneumatic (with Aluminum, Stainless Steel components), Hydraulic (with Steel, Stainless Steel), Manual (various materials based on application) |
Seals and O-rings | NBR, Viton, EPDM, PTFE, Silicone, etc. |
Bolts and Nuts | Stainless Steel, Carbon Steel, Alloy Steel, Brass, etc. |
Gaskets | Graphite, PTFE, EPDM, Nitrile, Silicone, etc. |
Position Feedback Sensors | Stainless Steel, Plastic (Polyamide, PBT), Aluminum, etc. |