Ball Valves vs. Globe Valves

The Application of Ball Valves vs. Globe Valves
In the realm of valve selection, the comparison between ball valves vs. globe valves is crucial. Globe valves feature a linear motion stem and a disc, ideal for throttling applications and providing precise flow control. On the other hand, ball valves offer a quarter-turn operation with a spherical closure element, enabling quick shutoff and low maintenance. While ball vs. globe valves differ in operation, each has distinct advantages. Cameron, a trusted brand, provides a comprehensive range of both globe and ball valves, catering to diverse industrial needs. Whether it’s the precise flow regulation of a globe valve or the rapid on/off action of a ball valve, Cameron ensures reliability and efficiency in fluid control systems.
ball valve vs globe valve
globe valve vs ball valve
globe vs ball valve
globe valves vs ball valves
ball valve vs gate valve vs globe valve
What Are The Types Of Steam Jacketed Globe Valves?
Types of Ball Valves:
- Floating Ball Valve: In this type, the ball is not fixed to the stem, allowing it to float slightly. This design ensures reliable sealing even in low-pressure applications.
- Trunnion Mounted Ball Valve: These valves have the ball supported by trunnions to reduce friction during operation, making them suitable for high-pressure applications.
- Top Entry Ball Valve: Top entry ball valves feature a removable bonnet, allowing easy access to the internals for maintenance or repair without removing the valve from the pipeline.
- Split Body Ball Valve: Split body ball valves have a two-piece or three-piece body design, facilitating easy maintenance by allowing disassembly of the valve body into separate parts.
Types of Globe Valves:
- Straight Pattern Globe Valve: This type has a linear flow path, with the stem and disc moving in a straight line perpendicular to the flow direction. It’s suitable for general-purpose applications and offers good throttling capabilities.
- Angle Pattern Globe Valve: Angle pattern globe valves have an angled body design, allowing the flow path to change direction. They are often used in applications where space is limited or where the flow needs to be redirected.
- Bellows-sealed Globe Valve: Bellows-sealed globe valves feature a bellows assembly that provides a hermetic seal around the valve stem, preventing leakage to the atmosphere. They are commonly used in applications where fugitive emissions need to be minimized.
- Pressure Seal Globe Valve: Pressure seal globe valves are designed to handle high-pressure and high-temperature applications. They feature a unique pressure seal bonnet design that enhances sealing performance under extreme conditions.
What Is Ball Valves vs. Globe Valves?
Ball valves vs. globe valves differ in design and function. Ball valves utilize a spherical disc to control flow, providing quick on/off functionality and minimal pressure drop. In contrast, globe valves employ a linear motion disc for precise flow regulation and throttling. When considering the CV of a valve and calculating CV of control valve, it’s essential to recognize their distinct characteristics to select the most suitable option for specific applications.
How Does Ball Valves vs. Globe Valves?
Ball valves operate by rotating a spherical ball with a hole through it to control flow. When the ball is aligned with the pipe, flow is allowed, and when perpendicular, flow is blocked. Globe valves, on the other hand, regulate flow by moving a plug or disc up and down against the flow direction, providing precise control over fluid flow rates.
Features of Ball Valves vs. Globe Valves
- Flow Control:
- Ball Valves: Offer quick on/off control, suitable for applications requiring rapid shut-off or minimal pressure drop.
- Globe Valves: Provide precise throttling capabilities, ideal for regulating flow rates and achieving accurate control.
- Design:
- Ball Valves: Feature a spherical disc that rotates to open or close the valve, allowing for efficient flow regulation.
- Globe Valves: Utilize a linear motion disc or plug, moving perpendicular to the flow direction to adjust flow rates with precision.
- Pressure Drop:
- Ball Valves: Typically have a lower pressure drop compared to globe valves due to their streamlined flow path.
- Globe Valves: May exhibit a higher pressure drop, particularly when partially open, due to the flow redirection caused by the disc movement.
- Application:
- Ball Valves: Commonly used in applications requiring rapid shut-off, such as pipelines, tanks, and isolation duties.
- Globe Valves: Preferred for applications where precise flow control is essential, such as throttling, regulating, and controlling flow rates in pipelines and process systems.
Advantages and Disadvantages of Ball Valves vs. Globe Valves
- Advantages:
- Ball Valves:
- Quick On/Off Operation: Ball valves offer rapid shut-off capability, making them suitable for emergency situations or where quick action is needed.
- Low Pressure Drop: Due to their streamlined flow path, ball valves typically exhibit lower pressure drop compared to globe valves, ensuring efficient flow.
- Minimal Maintenance: With fewer moving parts, ball valves require less maintenance and are less prone to failure, resulting in reduced downtime and operational costs.
- Versatility: Ball valves are suitable for a wide range of applications, including isolation, throttling, and control, making them versatile in various industries.
- Globe Valves:
- Precise Flow Control: Globe valves provide precise throttling capabilities, allowing for accurate regulation of flow rates and pressure.
- High Sealing Integrity: The linear motion of the disc ensures tight sealing against the valve seat, minimizing the risk of leakage even under high-pressure conditions.
- Durability: Globe valves are known for their robust construction and long service life, particularly in applications requiring frequent operation and high-cycle duty.
- Suitable for High-Temperature Applications: Globe valves are often preferred for high-temperature and high-pressure applications due to their reliable sealing and robust design.
- Ball Valves:
- Disadvantages:
- Ball Valves:
- Limited Control: Ball valves are less suitable for applications requiring precise flow regulation or throttling, as their on/off operation does not allow fine adjustments.
- Potential Cavitation: In high-pressure drop applications, ball valves may be susceptible to cavitation, leading to erosion and damage to the valve internals.
- Reduced Flow Capacity: In partially open positions, ball valves may exhibit reduced flow capacity compared to globe valves, potentially limiting their suitability for certain applications.
- Globe Valves:
- Higher Pressure Drop: Globe valves typically have a higher pressure drop compared to ball valves, resulting in increased energy consumption and reduced efficiency in some applications.
- Slower Operation: The linear motion of the disc in globe valves results in slower operation compared to the quick on/off action of ball valves, which may be disadvantageous in certain scenarios requiring rapid shut-off.
- Complex Design: Globe valves have a more complex design with additional components such as stems, discs, and seats, which may increase the risk of maintenance issues and require more frequent servicing.
- Ball Valves:
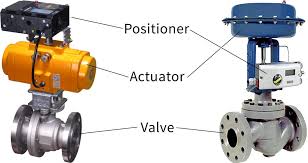
The Specifications of Ball Valves vs. Globe Valves
Specification | Value |
---|---|
Type | Globe Valve |
Ball Material | Not Applicable (Globe Valve) |
Attachment Type | Threaded |
Thread Standard | ANSI B1.20.1 |
Thread Size | 1/2 inch |
Body Material | Stainless Steel |
Safe for Use With | Water, Oil, Gas |
Handle Type | Handwheel |
Handle Material | Cast Iron |
Maximum Working Pressure (psi) | 600 psi |
Maximum Working Pressure (bar) | 41.4 bar |
Operating Pressure | 10-400 psi |
The Installation Steps for Ball Valves vs. Globe Valves
Installation Steps for Ball Valves:
- Preparation: Gather necessary tools and equipment, including wrenches, pipe tape, and a pipe cutter.
- Shut off System: Ensure the system is shut off and depressurized to prevent accidents during installation.
- Positioning: Position the ball valve in the desired location within the pipeline, ensuring proper alignment with the flow direction indicated by the arrow on the valve body.
- Flange Connection: Align the valve flanges with the corresponding flanges on the pipeline and secure them with bolts tightened to the manufacturer’s specifications.
- Piping Connections: Connect the inlet and outlet piping to the valve using appropriate fittings, ensuring tight seals and leak-free connections.
- Testing: Conduct a pressure test on the system to check for leaks and ensure proper valve operation.
- Inspection: Verify that all connections are tight, and there are no visible signs of leaks before putting the system back into service.
Installation Steps for Globe Valves:
- Preparation: Gather necessary tools and equipment, including wrenches, gaskets, and pipe tape.
- System Shutdown: Ensure the system is shut off and depressurized to prevent accidents.
- Positioning: Position the globe valve in the desired location within the pipeline, ensuring proper alignment with the flow direction indicated by the arrow on the valve body.
- Flange Alignment: Align the valve flanges with the corresponding flanges on the pipeline, ensuring proper alignment for a leak-free connection.
- Flange Connection: Secure the valve to the pipeline by tightening the flange bolts to the manufacturer’s specifications.
- Piping Connections: Connect the inlet and outlet piping to the valve using suitable fittings and pipe tape to ensure tight seals.
- Pressure Test: Conduct a pressure test on the system to check for leaks and ensure proper valve operation.
- Final Checks: Verify all connections are tight, and there are no visible signs of leaks before putting the system back into service.
The Operation Theory of Ball Valves vs. Globe Valves
Operation Theory of Ball Valves:
- Functionality: Ball valves control flow by rotating a spherical ball with a bore through it. When the bore aligns with the pipeline, flow is permitted, and when perpendicular, flow is blocked.
- Flow Control: Ball valves provide quick on/off control, making them suitable for applications requiring rapid shut-off or minimal pressure drop.
- Low Maintenance: With fewer moving parts, ball valves require minimal maintenance and are less prone to failure, resulting in reduced downtime and operational costs.
Operation Theory of Globe Valves:
- Functionality: Globe valves regulate flow by moving a plug or disc in a linear motion perpendicular to the flow direction. This movement varies the flow area and controls the flow rate.
- Flow Regulation: Globe valves offer precise throttling capabilities, making them suitable for applications requiring accurate flow control and regulation.
- Tight Sealing: The linear motion of the plug or disc ensures tight sealing against the valve seat, minimizing the risk of leakage even under high-pressure conditions.
Ball Valve vs. Globe Valve Symbol:
- Ball Valve Symbol: The symbol for a ball valve typically consists of a circle with a perpendicular line passing through it, representing the ball inside the valve body. This symbol is often accompanied by an arrow indicating the direction of flow.
- Globe Valve Symbol: The symbol for a globe valve typically resembles a circle with a T-shaped line attached to it, representing the globe-shaped disc or plug and the stem. Like the ball valve symbol, it may also include an arrow indicating flow direction.
The Parameters Chart of Ball Valves vs. Globe Valves
Parameter | Ball Valve | Globe Valve |
---|---|---|
Type | Ball Valve | Globe Valve |
Ball Material | Stainless Steel, Brass, Bronze, PVC, etc. | Not Applicable (Globe Valve) |
Body Material | Stainless Steel, Brass, Bronze, PVC, etc. | Stainless Steel, Cast Iron, Carbon Steel, etc. |
Seat Material | PTFE (Teflon), RPTFE, PEEK, Nylon, etc. | PTFE (Teflon), Metal, etc. |
Stem Material | Stainless Steel, Brass, Carbon Steel, etc. | Stainless Steel, Brass, etc. |
Handle Material | Stainless Steel, Carbon Steel, Plastic, etc. | Stainless Steel, Carbon Steel, Plastic, etc. |
Maximum Pressure | Varies based on size, material, and design. | Varies based on size, material, and design. |
Operating Temperature | Varies based on material and design. | Varies based on material and design. |