Forged Steel Ball Valve for Natural Gas Pipeline 2500LB Flange ends
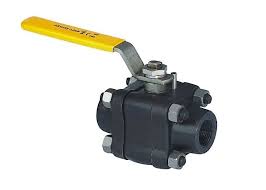
Standards
Design and Manufacture: API 6D
Face To Face: ASME B16.10
Flanged Ends: ASME B16.5
Test And Inspection: API 598
The Application of Forged Steel Ball Valve
Cameron, a renowned manufacturer in the industrial valve industry, offers a wide range of Forged Steel Ball Valve solutions, including the Apollo Forged Steel Ball Valve. These flanged ball valves are designed to deliver exceptional performance and reliability in demanding applications. The Forged Steel Ball Valve construction ensures superior strength, durability, and corrosion resistance, making them a popular choice for use in high-pressure, high-temperature, and harsh environments. Whether it’s for oil and gas, chemical processing, or power generation, Cameron’s Forged Steel Ball Valves provide the necessary flow control and isolation capabilities to meet the most challenging industry requirements.
What Are The Types Of Forged Steel Ball Valve?
- Full Port Forged Steel Ball Valve:
These valves feature a full-bore design, allowing for unrestricted flow and minimal pressure drop. They are commonly used in high-flow applications. - Reduced Port Forged Steel Ball Valve:
These valves have a smaller ball diameter compared to the pipe size, providing a more compact design while still maintaining good flow characteristics. - Trunnion-Mounted Forged Steel Ball Valve:
In this design, the ball is supported by trunnions (bearings) at the top and bottom, making it suitable for high-pressure and high-cycle applications. - Floating Forged Steel Ball Valve:
The ball in these valves is not fixed, allowing it to float and self-align, which can improve sealing performance and reduce the impact of pipe misalignment. - 3-Piece Forged Steel Ball Valve:
This design features a body split into three components, facilitating easier maintenance and repair by allowing the valve to be serviced without removing it from the pipeline.
What Is Forged Steel Ball Valve?
Forged Steel Ball Valves are a type of industrial valve widely used in a variety of industries, including oil and gas, chemical processing, power generation, and water treatment. These valves feature a ball as the primary flow control mechanism, which provides a reliable and efficient means of regulating fluid flow. The forged steel construction offers exceptional strength, durability, and corrosion resistance, making these valves well-suited for demanding operating environments. Forged Steel Ball Valves are known for their fast, quarter-turn operation, tight shutoff capabilities, and the ability to handle high pressures and temperatures. Their versatility and performance make them a popular choice for critical flow control applications across various industrial sectors.
How to Select the Right Forged Steel Ball Valve?
- Size and Port Configuration: Determine the appropriate valve size and whether a full port or reduced port design is required based on the flow rate and pipeline dimensions.
- Pressure Rating: Ensure the valve’s maximum working pressure and pressure rating are suitable for the system’s operating pressure requirements.
- Temperature Range: Verify that the valve materials can withstand the expected minimum and maximum operating temperatures.
- Body and Ball Material: Choose the appropriate forged steel alloy or other corrosion-resistant materials based on the compatibility with the media being handled.
- Sealing Requirements: Consider the valve’s sealing capabilities, such as bubble-tight shutoff, to meet the necessary isolation and leakage prevention needs.
- Actuation and Control: Decide if the valve requires manual operation or automated actuation for integration into a control system.
- Installation and Maintenance: Evaluate the valve’s design for ease of installation, accessibility for maintenance, and potential interchangeability with existing components.
Features of Forged Steel Ball Valve
- Size and Port Configuration: Determine the appropriate valve size and whether a full port or reduced port design is required based on the flow rate and pipeline dimensions.
- Pressure Rating: Ensure the valve’s maximum working pressure and pressure rating are suitable for the system’s operating pressure requirements.
- Temperature Range: Verify that the valve materials can withstand the expected minimum and maximum operating temperatures.
- Body and Ball Material: Choose the appropriate forged steel alloy or other corrosion-resistant materials based on the compatibility with the media being handled.
- Sealing Requirements: Consider the valve’s sealing capabilities, such as bubble-tight shutoff, to meet the necessary isolation and leakage prevention needs.
- Actuation and Control: Decide if the valve requires manual operation or automated actuation for integration into a control system.
- Installation and Maintenance: Evaluate the valve’s design for ease of installation, accessibility for maintenance, and potential interchangeability with existing components.
Advantages and Disadvantages of Forged Steel Ball Valve
Advantages of Forged Steel Ball Valve:
- Durability and Strength: The forged steel construction provides exceptional strength and resistance to physical damage, making these valves suitable for high-pressure and high-load applications.
- Corrosion Resistance: Depending on the alloy composition, Forged Steel Ball Valves can offer excellent corrosion resistance, prolonging the valve’s service life in harsh environments.
- Tight Shutoff: The ball-and-seat sealing mechanism can provide a near-perfect, bubble-tight seal when the valve is closed, ensuring effective isolation.
- Broad Temperature Range: Forged Steel Ball Valves can be designed to withstand a wide range of operating temperatures, from cryogenic to high-temperature conditions.
- Reliable Operation: The simple and robust design of Forged Steel Ball Valves contributes to their reliable performance and long service life.
- Easy Maintenance: The modular construction facilitates easy disassembly, inspection, and repair of the valve components.
Disadvantages of Forged Steel Ball Valve:
- Higher Cost: Forged Steel Ball Valves are generally more expensive compared to some other valve types, especially for larger sizes.
- Limited Throttling Ability: The ball mechanism is primarily designed for on/off control, with limited capabilities for precise flow throttling.
- Potential for Seat Damage: Frequent cycling or high-velocity flow can cause wear and damage to the valve seats over time, requiring periodic maintenance.
- Weight and Size: The forged steel construction can result in a heavier and larger valve design, which may pose challenges for installation and space constraints.
- Potential for Leakage: Improper maintenance or wear of the seals can lead to potential fluid leakage, which must be addressed through regular inspection and seal replacement.
The Specifications of Forged Steel Ball Valve
Specification | Detail |
---|---|
Type | 3-Piece Forged Steel Ball Valve |
Ball Material | 316 Stainless Steel |
Attachment Type | Flanged |
Thread Standard | ASME B16.5 |
Thread Size | 2 inch |
Body Material | ASTM A105 Forged Steel |
Safe for Use With | Oil, Gas, Water, Steam, Chemicals |
Handle Type | Lever |
Handle Material | Carbon Steel |
Maximum Working Pressure (psi) | 1,500 psi |
Maximum Working Pressure (bar) | 103 bar |
Operating Pressure | 0 – 1,500 psi (0 – 103 bar) |