What is Monoblock Ball Valve
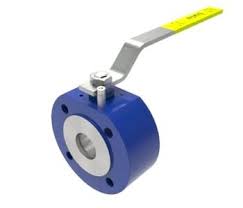
The Application of Monoblock Ball Valve
Monoblock ball valves are a popular choice for industrial applications due to their robust and compact design. Monoblock ball valves feature a one-piece body construction, providing superior strength and reliability, especially in high-pressure environments. High Pressure Monoblock Ball Valves are commonly used in the oil and gas, petrochemical, and power generation industries, where they are relied upon to safely control the flow of fluid and gas under extreme pressures. Leading Industrial Monoblock Ball Valve Brands, such as Cameron, offer a wide range of monoblock ball valve solutions engineered to meet the demanding requirements of these industries. The application of Monoblock Ball Valves extends beyond just high-pressure use, as they are also widely employed in general industrial pipework, ensuring reliable isolation and flow control across a variety of mediums and operating conditions.
What Are The Types Of Monoblock Ball Valve?
Full Port Monoblock Ball Valves: These valves have a bore diameter equal to the pipe size, allowing for unrestricted flow and minimal pressure drop. They are commonly used in high-flow applications.
Reduced Port Monoblock Ball Valves: These valves have a reduced bore diameter compared to the pipe size. This results in a slightly higher pressure drop but a more compact valve design.
High Performance Monoblock Ball Valves: Engineered for severe service, these valves feature enhanced design elements like blowout-proof stems, live-loaded stem seals, and anti-static devices. They are ideal for critical applications with high pressure, temperature, or corrosive media.
Trunnion-Mounted Monoblock Ball Valves: The ball is supported on both sides by trunnions, providing increased stability and torque capability. This design is well-suited for larger valve sizes up to 48 inches.
Floating Ball Monoblock Ball Valves: The ball is not fixed, but instead “floats” on the seats, allowing it to self-align for tight sealing even with pipeline misalignment or thermal expansion.
Multi-Port Monoblock Ball Valves: These specialized valves have multiple inlet and outlet ports, allowing them to direct flow to different pipelines with a single valve.
The specific type of monoblock ball valve selected will depend on the application requirements in terms of size, pressure, temperature, media, and flow characteristics. Leading manufacturers like Cameron offer a comprehensive range of monoblock ball valve solutions to meet diverse industrial needs.
What Is Monoblock Ball Valve?
A Monoblock Ball Valve is a type of industrial valve that features a one-piece body construction, eliminating the need for separate body and end connections. This robust design provides superior strength and reliability, making monoblock ball valves a popular choice for applications requiring high-pressure and high-flow control. Unlike traditional ball valves with multiple components, the monoblock design integrates the ball, stem, and body into a single, streamlined unit. This simplifies installation, reduces potential leak points, and enhances the overall durability of the valve. Monoblock ball valves are commonly used in industries such as oil and gas, petrochemicals, power generation, and general industrial processes, where they play a critical role in isolating, regulating, and protecting mission-critical equipment and pipelines.
How to Select the Right Monoblock Ball Valve?
When selecting the appropriate Monoblock Ball Valve for an application, there are several key factors to consider. The first and most crucial is the operating pressure and temperature range, as the valve must be rated to safely withstand the expected service conditions. Next, the size and flow capacity of the valve should match the pipeline requirements to ensure efficient and unobstructed fluid or gas transfer. Material compatibility with the media is also essential, as monoblock ball valves are available in a variety of corrosion-resistant alloys to handle a wide range of aggressive substances. Other important criteria include end connection type, actuation method, and any special features required, such as fire-safe design or fugitive emission control. By carefully evaluating these parameters, engineers can select the optimal monoblock ball valve solution to meet the unique demands of their industrial process or system.
Features of Monoblock Ball Valve
One-Piece Construction
The defining feature of a Monoblock Ball Valve is its single-piece body design, which eliminates the need for separate body and end connections, reducing potential leak points and improving overall reliability.
High Pressure Capability
Due to their robust construction, monoblock ball valves are well-suited for high-pressure applications, able to withstand extreme operating conditions in industries like oil and gas, petrochemicals, and power generation.
Compact Size
The integrated design of monoblock ball valves allows for a more compact and space-saving valve footprint compared to traditional multi-piece ball valve configurations.
Corrosion Resistance
Monoblock ball valves are available in a variety of corrosion-resistant materials, such as stainless steel and exotic alloys, enabling them to handle aggressive media and harsh environments.
Ease of Installation
The one-piece body design of monoblock ball valves simplifies installation, as there is no need to align and connect separate components during the valve commissioning process.
Advantages and Disadvantages of Monoblock Ball Valve
Advantages of Monoblock Ball Valves:
Improved Reliability: The one-piece construction of monoblock ball valves eliminates potential leak points, enhancing overall reliability and reducing the risk of costly failures.
Enhanced Durability: The robust design of monoblock ball valves allows them to withstand high pressures, temperatures, and corrosive media, making them well-suited for demanding industrial applications.
Compact Size: The integrated body design of monoblock ball valves results in a smaller footprint, allowing for easier installation in space-constrained environments.
Simplified Maintenance: With fewer components, monoblock ball valves require less disassembly and maintenance compared to traditional multi-piece ball valve designs.
Disadvantages of Monoblock Ball Valves:
Limited Sizes: Monoblock ball valves are generally available in smaller sizes, typically up to 24 inches in diameter, limiting their use in larger pipeline applications.
Higher Cost: Due to their specialized manufacturing process, monoblock ball valves can be more expensive than their multi-piece counterparts.
Reduced Flow Capacity: Depending on the port size, monoblock ball valves may have a slightly lower flow capacity compared to full-bore ball valves.
Potential for Thermal Expansion Issues: The one-piece design of monoblock ball valves can make them more susceptible to issues related to thermal expansion in certain applications.
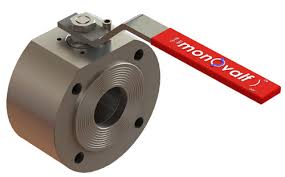
The Specifications of Monoblock Ball Valve
Specification | Details |
---|---|
Type | Full Port Monoblock Ball Valve |
Ball Material | 316 Stainless Steel |
Attachment Type | Threaded |
Thread Standard | NPT |
Thread Size | 1/2 inch |
Body Material | 316 Stainless Steel |
Safe for Use With | Water, Oil, Air, Gas |
Handle Type | Lever |
Handle Material | Stainless Steel |
Maximum Working Pressure (psi) | 1000 |
Maximum Working Pressure (bar) | 69 |
Operating Pressure | 800 psi (55 bar) |
The Installation Steps for Monoblock Ball Valve
1. Prepare the Pipe Connections
Ensure the pipe connections are clean, free of debris, and properly aligned to accept the valve. Apply a suitable thread sealant or tape to the pipe threads.
2. Position the Valve
Carefully insert the monoblock ball valve into the pipe system, making sure the flow direction arrow on the valve body matches the intended direction of fluid flow.
3. Tighten the Connections
Using a wrench, tighten the valve’s threaded connections to the recommended torque specification, typically between 40-60 ft-lbs (54-81 Nm) for a 1/2 inch NPT valve.
4. Verify Valve Orientation
Confirm that the valve’s handle is in the desired open or closed position, with the handle aligned properly for easy access and operation.
5. Perform Leak Testing
Pressurize the system and check all valve connections for any leaks. Tighten the connections further if necessary to ensure a proper seal.
6. Cycle the Valve
Operate the valve through several full open-close cycles to ensure smooth, unobstructed movement and proper functionality.
7. Document the Installation
Record the valve’s location, size, model number, and other relevant information for future reference and maintenance purposes.
The Operation Theory of Monoblock Ball Valve
Operation Theory of Monoblock Ball Valve
The operation of a monoblock ball valve is based on a simple but effective mechanism. The valve’s main component is a spherical ball with a bore that aligns with the pipe flow when the valve is open. To operate the valve, the ball rotates 90 degrees between the open and closed positions, either allowing or blocking the fluid flow through the valve.
The one-piece body design of the monoblock valve eliminates the need for separate components, simplifying the operation and reducing potential leak points. The tight sealing between the ball and the valve seats is maintained by the application of torque to the valve stem, which presses the ball against the seats.
When the valve is in the open position, the bore of the ball is aligned with the pipe, allowing unobstructed flow. Rotating the valve handle 90 degrees turns the ball to the closed position, where the solid portion of the ball blocks the flow path.
Petrochemical Monoblock Ball Valve Selection
Petrochemical applications often require monoblock ball valves that can withstand high pressures, temperatures, and corrosive media. Key considerations for selecting the right petrochemical monoblock ball valve include:
- Material compatibility with the process fluid (e.g., stainless steel, Hastelloy, or other corrosion-resistant alloys)
- Pressure rating (typically up to 1,500 psi or 103 bar)
- Temperature range (often from -40°C to 200°C/-40°F to 392°F)
- Fire-safe design for enhanced safety
- Fugitive emission control for environmentally-conscious operations
Stainless Steel Monoblock Ball Valve
Stainless steel monoblock ball valves are a popular choice across a wide range of industries due to their excellent corrosion resistance and durability. Common stainless steel alloys used in monoblock valve construction include 316/316L and 304/304L. These valves offer the following benefits:
- Corrosion resistance to handle aggressive chemicals, acids, and other harsh media
- High strength and wear resistance for long service life
- Suitability for a variety of process conditions, including high temperatures and pressures
- Easy maintenance and cleaning due to the smooth, non-porous stainless steel surfaces
- Compliance with industry standards and regulations for use in critical applications