Industrial Globe Valves
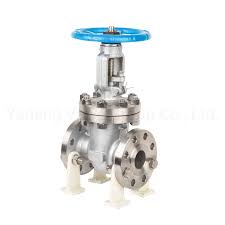
The Application of Industrial Globe Valves
Introducing Cameron’s superior range of industrial globe valves, meticulously engineered for diverse applications across industries. Globe valves stand out for their precise flow control capabilities, offering advantages over other valve types like gate valves and ball valves. While globe valves provide finer control and throttling of flow compared to gate valves, they also exhibit better sealing properties. In contrast, when compared to ball valves, globe valves excel in regulating flow rates with greater accuracy, making them ideal for applications requiring precise fluid control. Cameron’s commitment to quality ensures that our industrial globe valves meet the most stringent industry standards, providing unmatched reliability and performance in critical operations. Trust Cameron for superior solutions tailored to your industrial needs.
What Are The Types Of Industrial Globe Valves?
- Angle Globe Valves: These valves have an angled body design, allowing for easier installation in tight spaces and providing efficient flow control.
- Straight Globe Valves: Also known as “T-pattern” globe valves, these valves have a straight-through flow path, offering optimal flow characteristics and minimal pressure drop.
- Bellows Globe Valves: These valves feature a bellows seal that provides a secondary stem seal, ensuring leak-free performance in demanding applications and hazardous environments.
- Pressure Seal Globe Valves: Pressure seal globe valves are designed for high-pressure applications, featuring a self-sealing design that enhances reliability and safety under extreme pressure conditions.
- Cryogenic Globe Valves: Specifically designed for low-temperature applications, cryogenic globe valves maintain efficient flow control even at extremely low temperatures, ensuring reliable operation in cryogenic systems.
What Is Industrial Globe Valves?
Industrial globe valves are essential components used in various industries to control the flow of fluids within a pipeline. These valves feature a globe-shaped body with an internal mechanism that regulates the flow by raising or lowering a disc or plug against the flow path. They are commonly used to throttle, stop, or regulate the flow of liquids, gases, and steam in pipelines. Industrial globe valves are known for their versatility, reliability, and precise flow control capabilities, making them indispensable in applications where accurate flow regulation is critical. They find widespread use in industries such as oil and gas, petrochemicals, power generation, water treatment, and manufacturing.
How to Select the Right Industrial Globe Valves?
When selecting the right industrial globe valves, consider factors such as fluid type, pressure, temperature, and flow rate. Evaluate the specific requirements of your application and choose valves with suitable materials, design, and specifications to ensure optimal performance and reliability.
Features of Industrial Globe Valves
- Precise Flow Control:
- Industrial globe valves offer precise regulation of fluid flow, allowing for accurate adjustment of flow rates to meet specific process requirements.
- Versatility:
- These valves are versatile and can be used in a wide range of applications across various industries, including oil and gas, petrochemicals, power generation, and water treatment.
- Excellent Sealing:
- Globe valves provide excellent sealing properties, minimizing the risk of leakage and ensuring tight shut-off when the valve is closed.
- Bidirectional Flow:
- Unlike some other valve types, such as check valves, industrial globe valves allow for bidirectional flow, making them suitable for both forward and reverse flow applications.
- Durable Construction:
- Constructed from high-quality materials such as stainless steel, carbon steel, and alloy steel, globe valves are durable and resistant to corrosion, erosion, and wear.
- Easy Maintenance:
- These valves are designed for easy maintenance, with accessible components and straightforward repair procedures, minimizing downtime and maintenance costs.
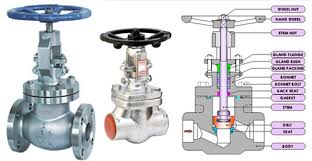
Advantages and Disadvantages of Industrial Globe Valves
Advantages:
- Precise Flow Control: Industrial globe valves offer precise regulation of flow rates, making them ideal for applications requiring accurate flow adjustments.
- Versatility: These valves can be used in a wide range of industries and applications, thanks to their adaptable design and capabilities.
- Excellent Sealing: Globe valves provide reliable sealing properties, minimizing the risk of leakage and ensuring tight shut-off when closed.
Disadvantages:
- Pressure Drop: Globe valves can cause a significant pressure drop across the valve, which may affect system efficiency, especially in high-flow applications.
- Complex Design: The internal components of globe valves can be more complex compared to other valve types, potentially increasing the risk of maintenance issues or component failure.
- Higher Cost: Globe valves tend to be more expensive than some other valve types, which may impact initial procurement costs.
The Specifications of Industrial Globe Valves
Specification | Details |
---|---|
Type | Globe Valve |
Body Material | Cast Iron, Carbon Steel, Stainless Steel, etc. |
Ball Material | Stainless Steel, Carbon Steel, Alloy Steel, etc. |
Attachment Type | Flanged, Threaded, Welded |
Thread Standard | ANSI B1.20.1, BSPT, DIN, JIS, etc. |
Thread Size | 1/2 inch – 12 inches |
Safe for Use With | Water, Steam, Oil, Gas, Chemicals, etc. |
Handle Type | Handwheel, Gear Operated, Actuated |
Handle Material | Stainless Steel, Carbon Steel, Aluminum, etc. |
Maximum Working Pressure (psi) | Up to 2500 psi |
Maximum Working Pressure (bar) | Up to 172.37 bar |
Operating Pressure | 0 psi – Maximum Working Pressure |
The Installation Steps for Industrial Globe Valves
- Preparation:
- Gather all necessary tools and equipment, including wrenches, gaskets, and pipe thread sealant.
- Ensure the work area is clean, dry, and free from debris.
- Valve Positioning:
- Identify the optimal location for the globe valve within the piping system, considering accessibility and operational requirements.
- Valve Mounting:
- Securely mount the globe valve to the pipeline using appropriate bolts and gaskets.
- Ensure proper alignment of the valve to facilitate smooth operation.
- Attachment Connection:
- Connect the globe valve to the piping system using flanged, threaded, or welded connections, based on the valve design and system requirements.
- Apply pipe thread sealant or gaskets to ensure a secure seal.
- Actuator Installation:
- If the globe valve includes an actuator, install it according to the manufacturer’s instructions.
- Connect any necessary wiring or tubing for actuation and control.
- Pressure Testing:
- Conduct a pressure test on the valve and piping system to ensure there are no leaks or defects.
- Gradually increase pressure and monitor for leaks, following industry-standard procedures.
- Final Inspection:
- Inspect the installed globe valve for proper alignment, tightness of connections, and overall functionality.
- Verify that all components are installed correctly and securely.
- Documentation:
- Maintain detailed records of the installation process, including valve specifications, pressure test results, and any adjustments made during installation.
- Update system documentation and diagrams to reflect the newly installed globe valve.
- Training:
- Provide training to relevant personnel on the operation, maintenance, and troubleshooting of the globe valve system.
The Operation Theory of Industrial Globe Valves
The operation theory of industrial globe valves revolves around their unique design, which allows for precise flow control within pipelines. Unlike gate valves, which use a wedge-shaped gate to control flow, globe valves utilize a disc or plug that moves perpendicular to the flow direction. This movement regulates flow by either allowing or obstructing the passage of fluid through the valve.
When comparing globe valves to ball valves, the key difference lies in their internal mechanisms. While ball valves use a spherical disc to control flow, globe valves employ a linear motion disc or plug. This design feature enables globe valves to provide more accurate throttling and regulation of flow rates, making them suitable for applications where precise control is essential.
In summary, the operation theory of industrial globe valves centers on their ability to regulate flow through the movement of a disc or plug perpendicular to the flow direction. Compared to gate valves and ball valves, globe valves offer superior flow control and are ideal for applications requiring precise adjustment of flow rates.
The Parameters Chart of Industrial Globe Valves
Parameter | Material |
---|---|
Valve Type | Globe Valve |
Body Material | Cast Iron, Carbon Steel, Stainless Steel, Alloy Steel, Bronze, etc. |
Disc Material | Stainless Steel, Carbon Steel, Alloy Steel, Bronze, etc. |
Seat Material | Stainless Steel, Carbon Steel, Alloy Steel, Bronze, etc. |
Stem Material | Stainless Steel, Carbon Steel, Alloy Steel, etc. |
Bonnet Material | Cast Iron, Carbon Steel, Stainless Steel, Alloy Steel, etc. |
Connection Type | Flanged, Threaded, Welded, Socket Weld, etc. |
Packing Material | PTFE, Graphite, Braided Packing, etc. |
Gasket Material | Graphite, Spiral Wound, Non-Asbestos, etc. |
Operating Mechanism | Handwheel, Gear Operated, Actuated, etc. |